We have heard of 3D printed toys, but who knew at some point, the U.S. Air Force will use the same technique to produce a metal part for B-52 bomber’s engine. This 3D printing upgrade will help to keep the plane in service until the late 2020s.
Additive manufacturing technology is providing easily-manufactured parts for rebuilding and renewing processes of the beast aircraft. The elements which went obsolete could now be produced in abundance using 3D printing. However, the Air Force is proceeding slowly to ensure it doesn’t push the tech too far to cause conceivably destructive results.
U.S. Air Force engineers at Tinker Air Force Base 3D printed an anti-icing gasket for the B-52s Pratt & Whitney TF33-P103 turbofan engine. The TF33 is the original engine installed on the B-52H bombers when they were first produced in the early 1960s. Each plane is powered by eight of these engines.
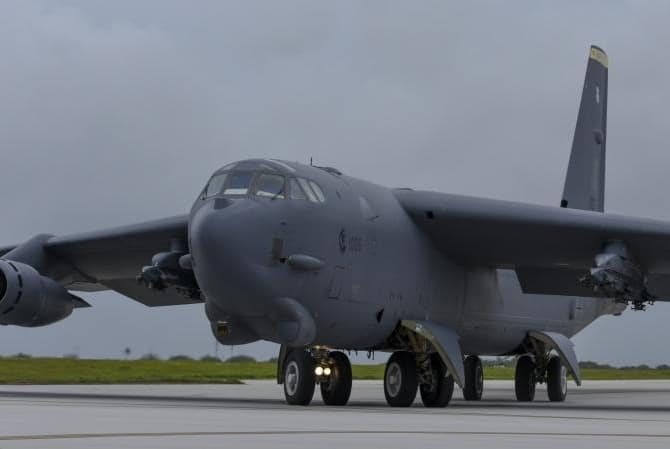
As the service’s aircraft fleet ages, spare parts inventories shorten and disappear. The contractors that build the parts may end production or even go out of business, that’s where additive manufacturing, can lend a helping hand. In the past, the only alternative way was cannibalizing the parts from grounded planes.
To build the new anti-ice gaskets for the TF-33s, the engineers took an OEM gasket and reverse-engineered it to print new ones. The Air Force has printed 30 parts till now, but it will possibly need a lot more, as its fleet of B-52s has a total of 608 engines.
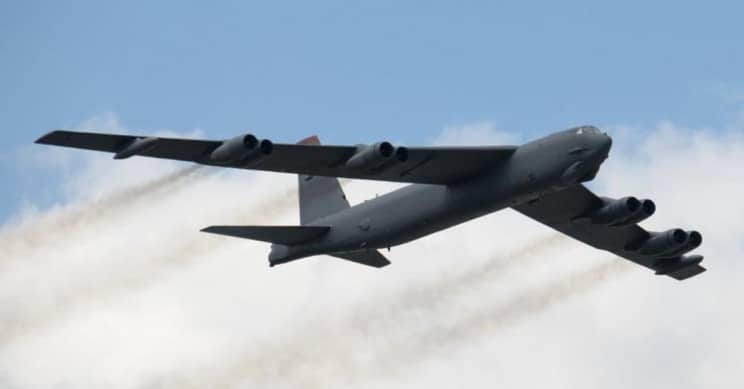
3D printing has helped to revive the old engines and supposedly will keep them flying until the Air Force installs completely new engines on the B-52 fleet later this decade, extending the fleet’s life span by 90 years.