Computer Numerical Control (CNC) machining is an integral cog in the engine of modern manufacturing. The popularity of CNC machines keeps growing due to their ability to automate the manufacturing process, and their market size is expected to hit USD $20,463 million in 2024. These clever machines carve out blocks of metal, plastic, wood, or other materials into incredibly precise shapes and parts.
Different machines offer varying numbers of axes, so it’s key to understand how they work when selecting the right CNC equipment. The axis count determines the complexity of parts you can produce and impacts the overall cost and operational needs.
Understanding the axes
Fundamentally, CNC machines operate along three core linear axes: X, Y, and Z. These refer to back-and-forth (X), left-and-right (Y), and up-and-down (Z) motions on flat planes. Extra rotating axes labeled A, B, and C introduce the ability to pivot around these linear axes.
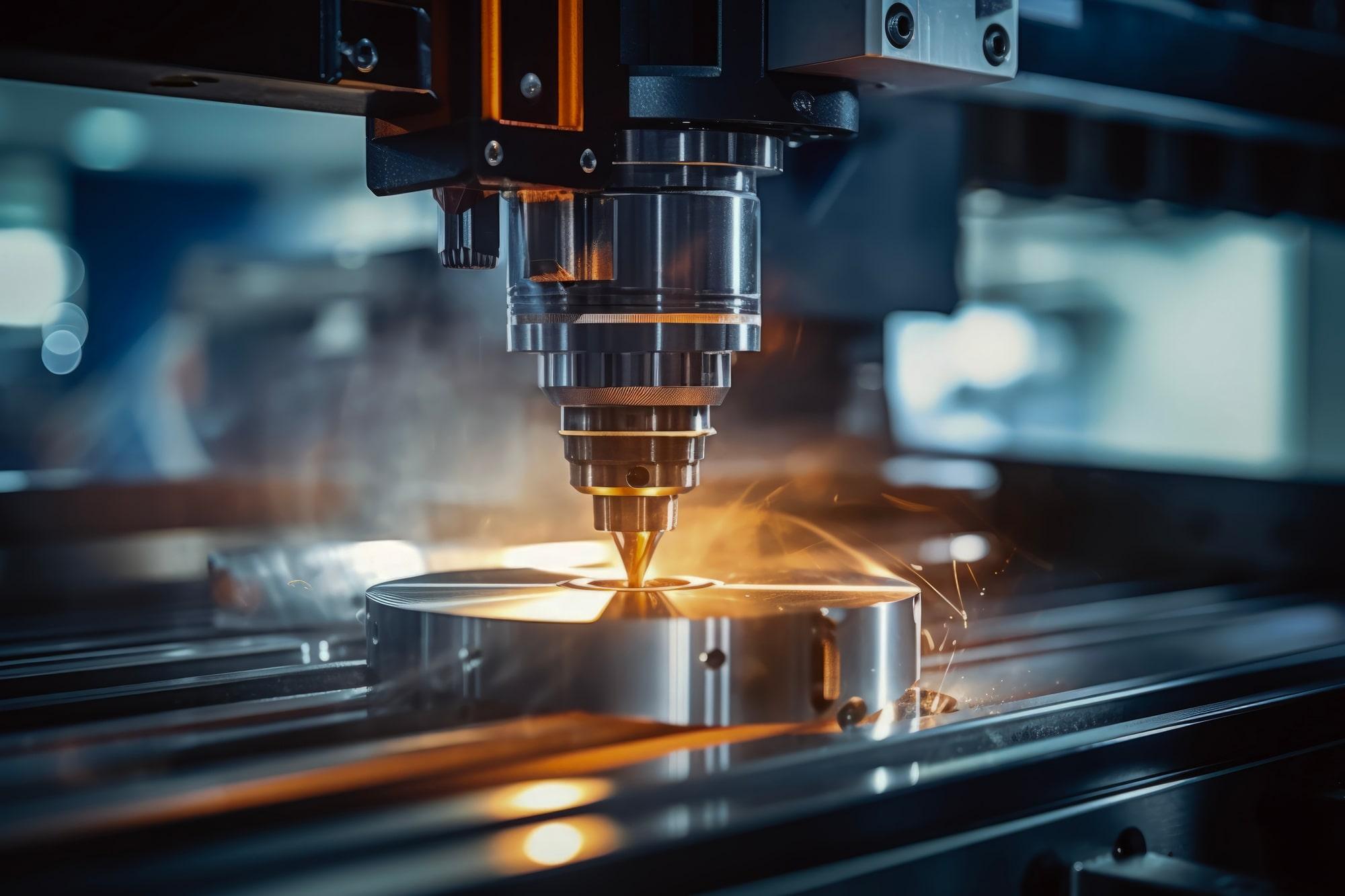
This crucial distinction between sliding and spinning opens the door for more nuanced manipulation of the workpiece, allowing intricate and detailed cuts. The properties of the axes are useful, especially for a manufacturer or a CNC service, to customize parts based on general tolerance, surface roughness, and material.
Common CNC machine axis configurations
The capabilities of CNC machines largely depend on their axis configurations. The number and type of axes dictate the complexity of parts the machine can produce. Here’s a quick look into the most common CNC machine axis layouts—3-axis, 4-axis, and 5-axis—and see how they stack up.
- 3-axis CNC machines
The 3-axis CNC machine lays the foundation for most CNC machining. As the name suggests, it can operate along the three primary X, Y, and Z linear axes. This flexibility allows the tool to shift horizontally, move in and out, and raise and drop vertically. With these basic motions, 3-axis machines can produce simple cut shapes and machined parts.
The simplicity and affordability of 3-axis CNC makes it accessible for all users, from hobbyists to production shops focusing on high-volume runs of standard parts. These machines shine at creating flat surfaces and can be used as metal fabricators or on plastics and wood—their versatility cements the 3-axis as a mainstay in small job shops.
However, limitations quickly emerge when dealing with intricate parts. Since motion is restricted to three axes, features not aligned to these planes require tedious manual repositioning of the workpiece. This not only slows production but also introduces potential inaccuracies. While suitable for simple components, the 3-axis design must be revised for work requiring tight tolerances or tricky geometries.
- 4-axis CNC machines
Expanding on the 3-axis foundation, 4-axis CNC machines introduce an additional rotating axis. Typically oriented vertically (designated the A or C axis), this fourth axis enables the workpiece to pivot and spin. The cutting tool can then approach from different angles without manual resets, making it easier to manufacture detailed 3D contours in a single setup.
This upgrade pays dividends when dealing with cylindrical parts or components requiring angled holes and complex cutouts. By reducing workpiece hand-positioning, 4-axis machining saves time and boosts precision.
Understandably, the costs run higher than the 3-axis, but the productivity and accuracy gains warrant consideration for applications like aerospace fittings, precision-turned parts, and intricate medical instruments like dental prostheses. Where complexity and tolerances are critical, a 4th axis facilitates efficient CNC machining.
- 5-axis CNC machines
At the apex of CNC technology sit 5-axis machines. With two additional rotating axes, the cutting tool can be oriented along virtually any direction in 3D space relative to the work surface. This exceptional freedom enables more complex part geometries to be produced in a single setup without resets.
5-axis CNC machining heightens accuracy while slashing production times by eliminating manual intervention and additional steps. The capacity to machine sophisticated contours, undercuts, and angles makes the 5-axis the go-to method for industries like aerospace, autos, and medical devices, where meticulous designs and tight tolerances are mandatory.
While the programming complexity and costs exceed lower axis-count machines, the manufacturing precision, efficiency, and design potential justify the challenges for advanced applications. Where production needs demand the creation of challenging components with intricate design elements, a 5-axis machine opens new doors.
Beyond basic axis counts
CNC machining technology continues to advance rapidly, far surpassing the capabilities of early 3-axis systems. Creative manufacturers find ways to stretch beyond existing constraints to boost precision, flexibility, and automation.
One key innovation is the tool orientation optimization. Optimizing tool orientation in five-axis CNC machining focuses on minimizing contour errors and avoiding interference, ensuring efficient and accurate machining. Predictions accurately forecast contour errors by accounting for the real feedrate, servo system dynamics, and motion characteristics.
This optimization turns complex constraints into simpler problems, significantly improving error reduction—experiments show decreases in tooltip and orientation errors by 52.2% and 75.6%, respectively. This approach streamlines the machining process, enhancing performance without the usual complications.
Conclusion
Understanding axis capabilities is crucial when selecting CNC solutions. From accessible 3-axis for basic parts to ultra-capable 5-axis for mission-critical components, matching machine functionality to production and design goals optimizes processes. As CNC constantly advances, keeping abreast of the latest axis innovations helps manufacturers leverage this revolutionary technology.