Researchers at Boston University have developed an innovative 3D-printing robot named MAMA BEAR (Mechanics of Additively Manufactured Architectures Bayesian Experimental Autonomous Researcher) that leverages artificial intelligence (AI) to advance material design. This project, undertaken for the US Army, aimed to create a shock-absorbing structure that surpasses human capabilities. Over the past three years, MAMA BEAR has continuously produced over 25,000 3D-printed structures, aiming to maximize mechanical energy absorption efficiency—an essential property for various applications such as safer helmets, packaging, and car bumpers.
Traditional trial-and-error methods are insufficient for investigating the vast possibilities at different length scales. To overcome this, the team at KABlab, part of the university’s College of Engineering, employed two innovative techniques. First, they developed nano-combinatorial methods using scanning probes to study and design small-scale materials. Second, they created autonomous research systems combining automation with machine learning to accelerate knowledge generation.
Since its inception in 2018, MAMA BEAR has undergone several modifications. By 2021, the robot was programmed to create shapes with the highest mechanical energy absorption efficiency. Utilizing recent advances in machine learning, the robot generated new insights from large datasets and more efficiently acquired smaller datasets. Throughout its continuous operation, the robot produced thousands of structures, demonstrating the necessity of creating numerous shapes due to the wide range of potential applications.
Keith Brown, an associate professor of mechanical engineering at Boston University, emphasized the practical implications of this extensive data library. It can significantly improve designs for car bumpers, packaging, and other equipment.
“You could draw from this library of data to make better car bumpers or packaging equipment, for example,” said Keith Brown. “We’re excited that there’s so much mechanical data here, that we’re using this to learn lessons about design more generally,” said Brown.
The research team achieved a notable breakthrough with MAMA BEAR producing a structure with 75 percent energy absorption efficiency, surpassing the previous maximum of 71 percent. The record-breaking structure was taller, thinner, and featured four petal-like points, surprising the researchers with its innovative design.
Collaborating with the US Army, the team applied their data to design new helmet padding for soldiers. This padding, differing from the record-breaking structure, has a softer center and shorter stature for enhanced comfort and effectiveness. The KABlab aims to highlight the importance of autonomous research, with Brown planning to continue interdisciplinary collaborations to assist scientists needing extensive testing of various structures and solutions.
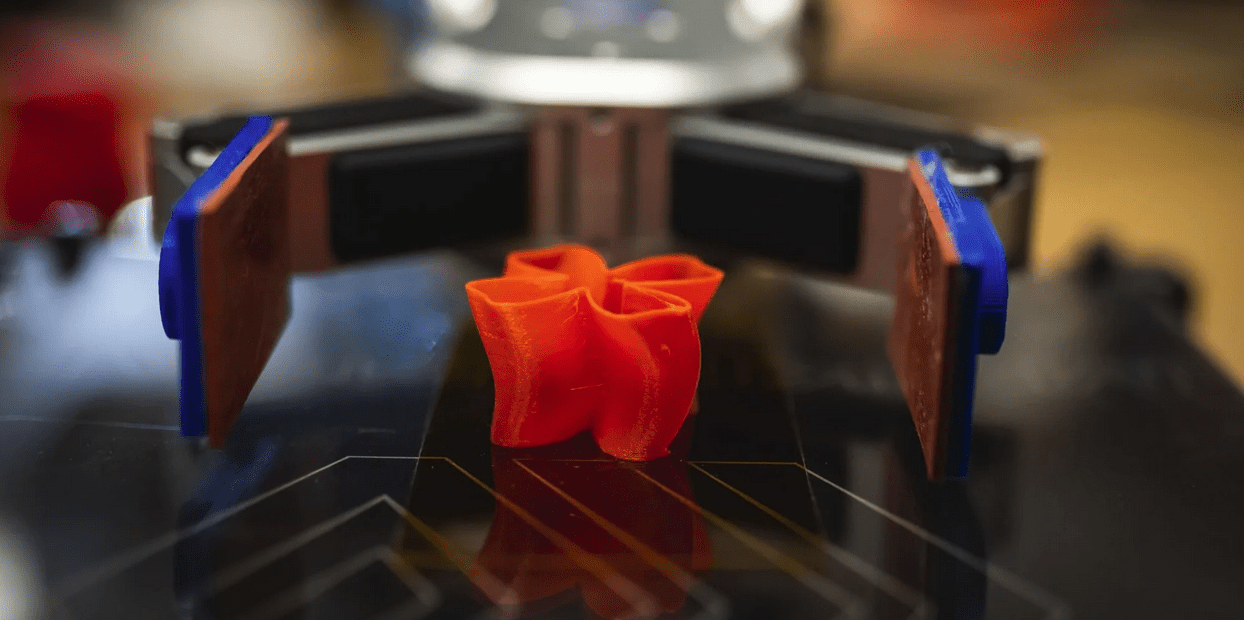
Despite achieving a record, the researchers acknowledge the potential for further advancements. MAMA BEAR will continue operating, pushing the boundaries of material design.
Brown emphasizes, “we have no ability to know if we’ve reached the maximum efficiency,” hinting at the possibility of surpassing it again.
The team is also exploring methods to recycle the 25,000 crushed pieces for further experiments by reloading them into 3D printers. Brown underscored the value of self-driving labs in performing experiments rapidly and efficiently, aiding in the accurate measurement of material properties like mechanical efficiency.
“We’re going to keep studying this system, because mechanical efficiency, like so many other material properties, is only accurately measured by experiment.
And using self-driving labs helps us pick the best experiments and perform them as fast as possible,” said Brown. The details of the team’s research were published in the journal Nature Communications.