Toyota, renowned for its dependable vehicles, places significant emphasis on the manufacturing process, recognizing the critical role of human workers alongside automated machinery. Despite the efficiency of the Toyota Production System, human workers are susceptible to accidents, particularly when interacting with heavy machinery. To enhance worker safety, Toyota innovated dummy fingers, fabricated at its headquarters in Toyota City, Japan, by Takeo Mori, a manager in the Manufacturing Engineering Department.

With the increasing prevalence of automation within factory settings, the potential for accidents involving human workers and heavy machinery rises. Particularly, injuries to hands and fingers present a notable risk in manufacturing environments, spanning from minor bruises to severe cuts.
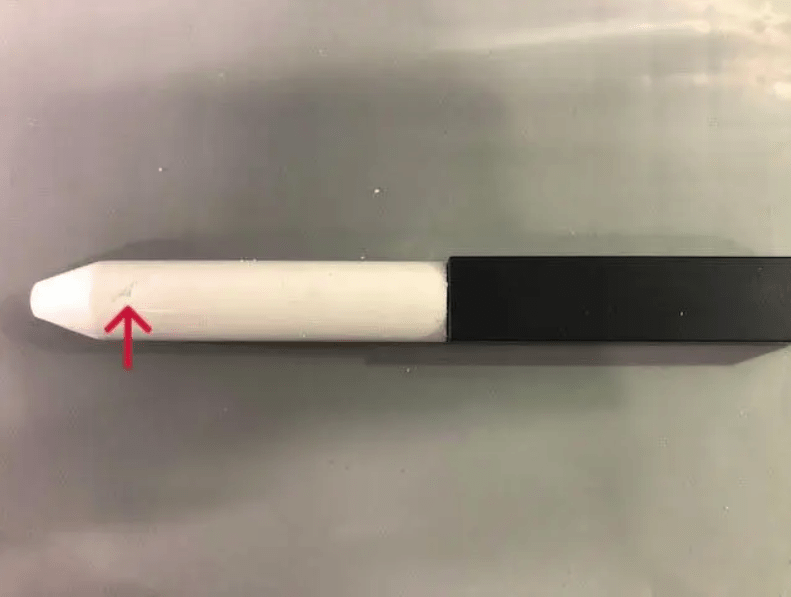
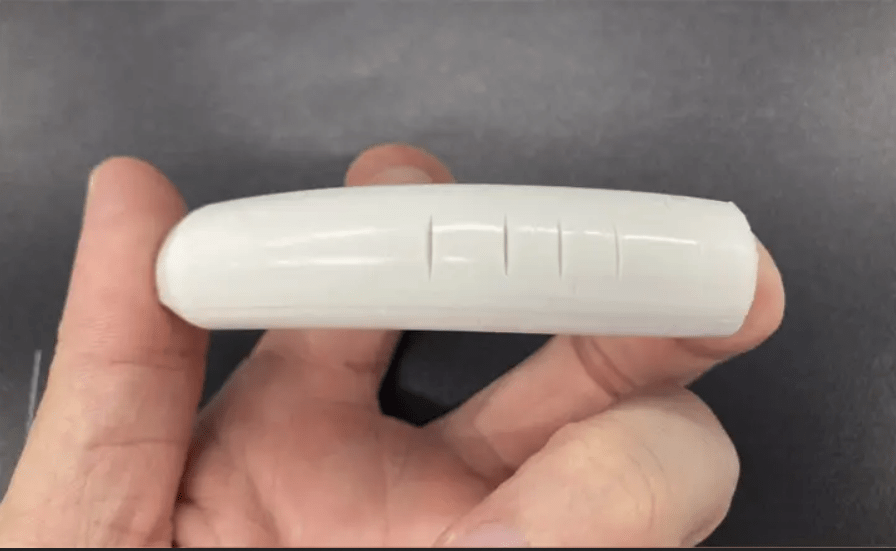
In response to this challenge and with a commitment to prioritizing worker safety, Toyota initiated an innovative project to fabricate dummy fingers. These synthetic appendages, conceptualized and manufactured at Toyota’s headquarters in Toyota City, Japan, symbolize a proactive strategy to mitigate workplace perils. Spearheading this endeavor is Takeo Mori, a manager within the Manufacturing Engineering Department, who collaborated with partners such as Panasonic and Nagoya University’s medical school to realize this endeavor.
The creation of dummy fingers represents a fusion of engineering prowess and medical knowledge. By utilizing materials like pig skin and stainless steel, Toyota engineers meticulously crafted these artificial digits to closely emulate the characteristics of human fingers. Diverse variants were produced to replicate different gender and age categories, ensuring comprehensive safety assessments across various demographics.

What distinguishes Toyota’s approach is its dedication to simplicity and pragmatism. While other companies may opt for intricate computer-based analytical methodologies, Toyota opted for an analog system that could be effortlessly implemented on-site without necessitating extensive training or specialized equipment. This choice underscores Toyota’s unwavering focus on practical solutions that can promptly enhance worker safety.
Beyond their immediate utility in manufacturing, dummy fingers have also contributed to the enhancement of vehicle components’ safety. By simulating real-life scenarios, such as incidents of finger entrapment in car doors, Toyota gains valuable insights that drive ongoing enhancements in vehicle safety features. Ranging from fortified tonneau covers to improved door mechanisms, these innovations exemplify Toyota’s holistic approach to safety across the automotive domain.
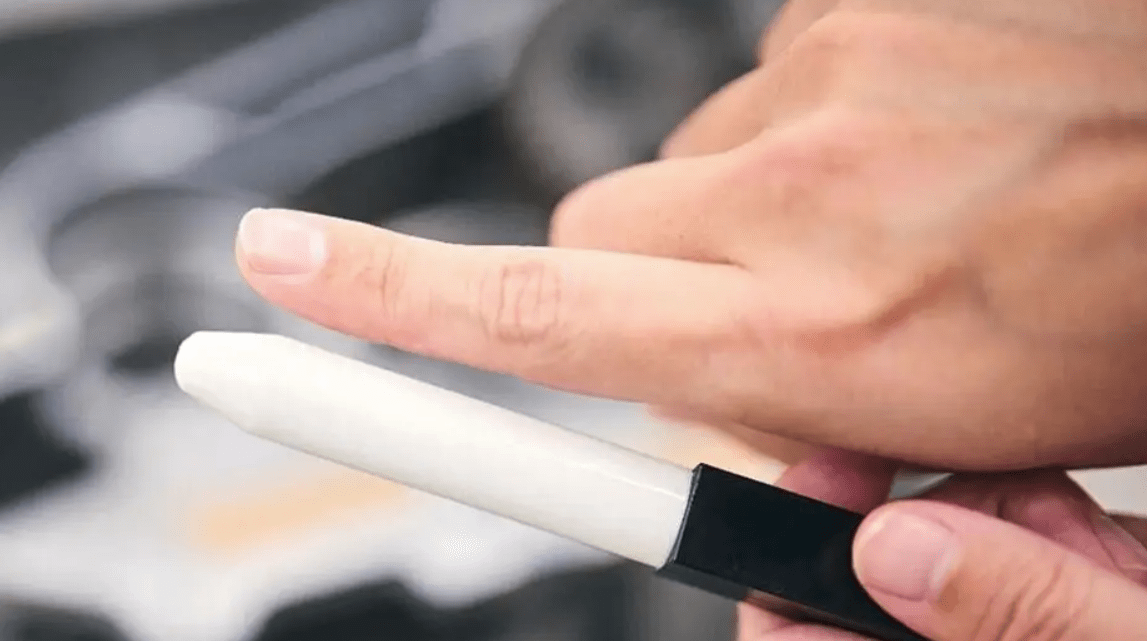
Toyota’s dedication to excellence and forward-thinking is epitomized by its allocation of resources towards the development of dummy fingers. Through a steadfast prioritization of worker safety and the cultivation of interdisciplinary collaboration, Toyota not only amplifies the efficiency of its manufacturing processes but also establishes a precedent for safety standards within the automotive domain.
As Toyota persists in its evolution and adaptation to dynamic technological landscapes, its unwavering commitment to solutions centered around human welfare persists, promising a future that is both safer and more sustainable for all.