Imperial College is pioneering the development of an incredibly small rocket thruster known as the ICE-Cube Thruster. This groundbreaking technology is so minuscule that its fabrication requires techniques initially designed for manufacturing silicon chips. While this may sound like an unusual approach, it addresses a critical need in the world of satellite technology.
In today’s era of space exploration, satellites weighing less than 10 kilograms, constituting about 90% of all satellite launches, have become increasingly prevalent. Some of these satellites are no larger than a typical smartphone. Consequently, creating components that meet the specific requirements of these CubeSats has proven to be a significant challenge. One of the most pressing issues is designing rocket thrusters that are not only small but also possess certain characteristics. These thrusters must be simple, unpressurized, low-power, and free from toxic materials.
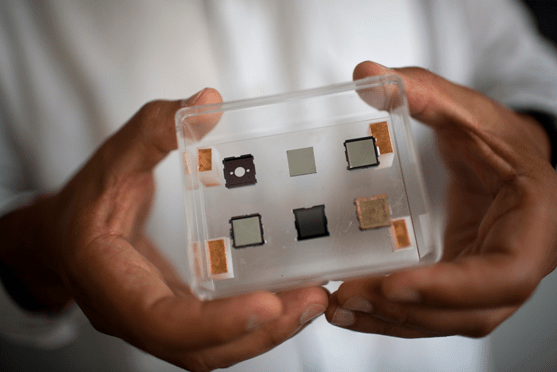
Funded by the European Space Agency (ESA), the ICE-Cube Thruster undeniably meets the criteria for small size. In fact, it is exceptionally tiny. The entire thruster chip’s length is roughly equivalent to that of a fingernail, with the combustion chamber and nozzle measuring a mere 1 millimeter in length. Despite its diminutive size, it operates efficiently, requiring only 20 watts of electric current.
During testing, it generated 1.25 millinewtons of thrust at a specific impulse of 185 seconds, which, when placed in perspective, is about half a billion times less powerful than the engines used on the Space Shuttle.
Nevertheless, what sets the ICE-Cube Thruster apart is its utilization of ordinary water as its propellant. Water is an incredibly safe choice, being non-explosive and non-flammable. The thruster employs onboard electric current to perform electrolysis, breaking down the water into hydrogen and oxygen. These gases are then directed into the combustion chamber, where they ignite to produce the thrust necessary for maneuvering the CubeSat.
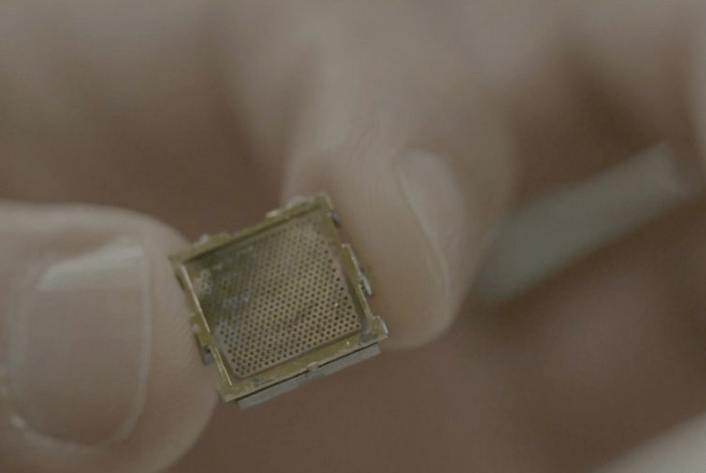
Not only is using water environmentally friendly, but it also reduces the satellite’s overall weight. There is no need for pressurized tanks to store the water, resulting in lighter and simpler storage and handling systems. However, fabricating the combustion chamber and nozzle for the thruster in what is essentially two dimensions proved to be a unique challenge.
To overcome this obstacle, the development team turned to the Micro-Electrical Mechanical Systems (MEMS) technique, typically used for machining silicon wafers with sub-micrometer precision in the manufacturing of processors.
While unconventional, this approach has proven highly effective. Not only does it accomplish the task at hand, but it is also scalable, allowing for the mass production of these minuscule thrusters. Consequently, the ICE-Cube Thruster represents a significant advancement in satellite propulsion technology, making space exploration more efficient and environmentally friendly. It also opens doors to new possibilities for future CubeSat missions, enabling them to perform complex maneuvers and expand our understanding of the cosmos.