Form Energy, a startup supported by influential figures such as Gates and Bezos, is poised to revolutionize the grid-level renewable energy storage landscape with its game-changing iron-air battery system. This cutting-edge technology promises extended-duration energy storage at a fraction of the cost of lithium batteries, paving the way for a more sustainable and economically viable approach to storing renewable energy.
To transition electrical grids toward 100% renewable energy, the need for smart, affordable, and environmentally friendly energy storage solutions becomes paramount. Grid operators seek practical methods to store surplus energy generated during off-peak periods and unleash it when demand surpasses supply. These storage capabilities must span various timescales, from daily grid smoothing to long-term storage to combat multi-day spells of adverse weather or reduced renewable energy generation.
Form Energy has focused its efforts on addressing long-duration energy storage challenges by introducing a modular battery solution centered around the iron rust cycle. By harnessing electricity, these compact battery modules efficiently convert iron oxide (rust) into metallic iron during the charging process, simultaneously releasing oxygen. During discharge, oxygen is reintroduced, transforming the metallic iron back into rust and liberating stored energy.
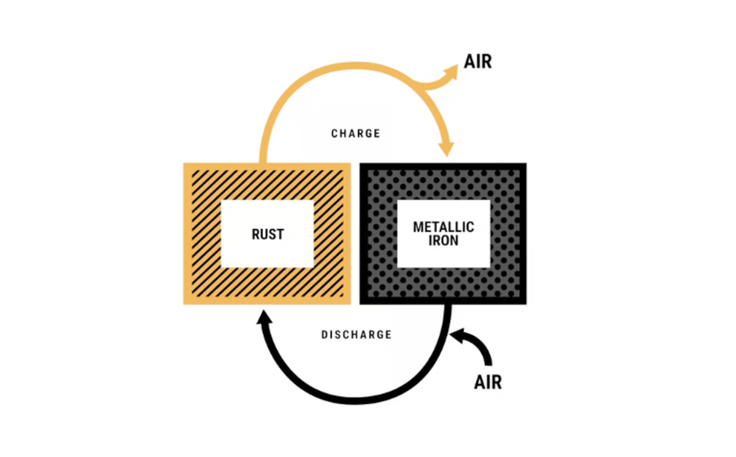
Although the reaction in iron-air batteries operates slower than lithium batteries’ rapid discharge, it remains impressively efficient. A full discharge cycle spans approximately 100 hours or just over four days, strategically aligning with the multi-day storage requirements necessary to counterbalance inclement weather conditions. However, it’s essential to consider that specific locations may experience variations in discharge durations due to localized weather patterns.
The advantages offered by iron-air batteries are both straightforward and compelling. Direct reduced iron, the most cost-effective iron variant primarily used in steelmaking, serves as the foundation for these batteries. It is abundantly available and poses no safety concerns. Likewise, water and air—two readily accessible elements—play essential roles in the battery’s operation.
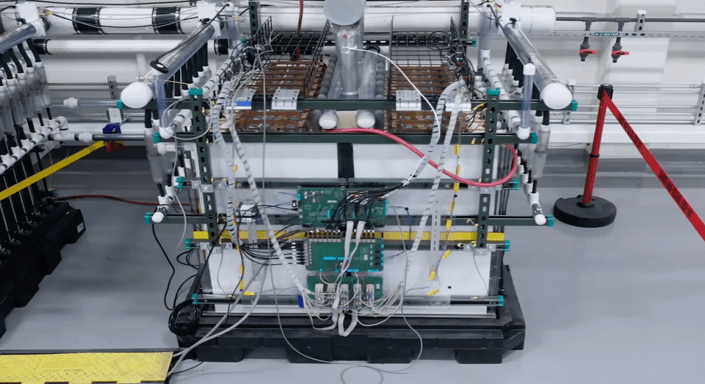
Furthermore, iron-air batteries boast a lengthy lifespan and are entirely recyclable, as the extracted iron components can be repurposed and sold. Iron-air batteries exhibit remarkable cost efficiency when considering the Levelized Cost of Storage (LCoS), amounting to approximately 10% of the expenses associated with lithium big battery arrays per stored and released kilowatt-hour.
Following the announcement of a groundbreaking $760 million manufacturing plant in West Virginia, Form Energy recently revealed an awe-inspiring demonstration project—a 10-megawatt/1-gigawatt-hour system set to be constructed near the Sherburne County Generating Station in Minnesota. The chosen site’s proximity to the Sherco Solar facility, one of the nation’s largest solar generation sites under development, adds strategic value. Xcel Energy, which owns the site, intends to replace its coal-fired power plants with iron-air batteries, leveraging existing transmission infrastructure while maintaining energy release costs comparable to those of coal-fired electricity.
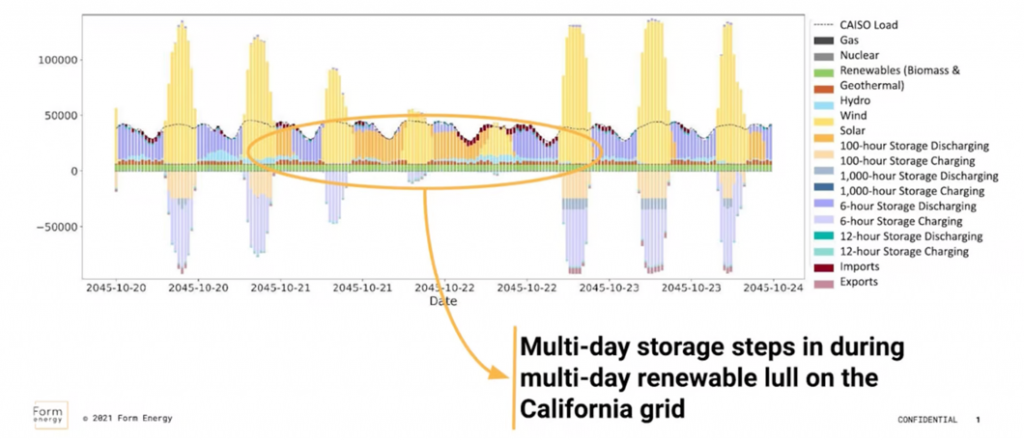
Bria Shea, Senior Vice President at Xcel, enthusiastically emphasizes the potential of multi-day battery storage in effectively harnessing renewable energy while ensuring grid reliability. The forthcoming demonstration project aligns seamlessly with Xcel’s commitment to achieving 100% carbon-free electricity. Construction is scheduled to commence within the next year, with the battery system expected to become operational by 2025.
Notably, Form Energy is also collaborating with Great River Energy on a smaller 1.5-megawatt system, further expanding its grid-connected projects within Minnesota.
Source: Form Energy