A Japanese startup called SkyDrive, unveiled its small, all-electric flying car at CES 2022 in Las Vegas earlier this month. Mark Blackwell, the company’s R&D strategy senior manager, stated that his firm is just a couple of years away from seeking final regulatory approval.
He assured that the car’s “design, structure, strength, and performance meet the necessary safety and environmental requirements.” As Head of SkyDrive’s R&D, Blackwell is responsible for getting the project (safely) across the finish line. He explained in an interview at CES how his team plans to accomplish the long-sought-after goal.
Mark Blackwell stated in an interview with Interesting Engineering that the question really is ‘Do we need to meet conventional aerospace failure rates, which is 10-9?’ And the answer is yes.
They are applying the safety precautions are being at the aircraft level, the system level, and the component level. They are also looking at what configurations are needed at the aircraft level to meet regulatory requirements for things like a bird strike, motor failures, battery failures, certain weather conditions.
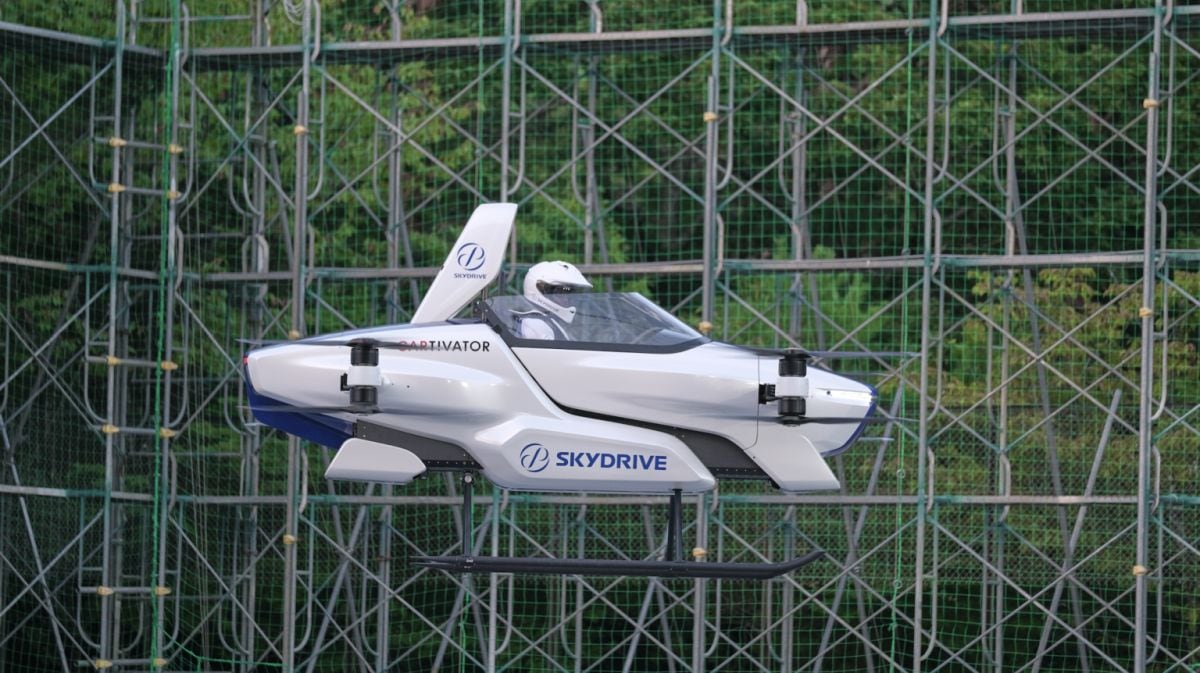
The company is striving to achieve certification by the end of 2024 and launch the vehicle in 2025 at the World Expo in Osaka. The public will give the users the experience of being in the novel car.
In industry, companies are great at mass manufactur[ing], and their work with materials is what we need to produce vehicles at scale. But the safety standards and the design processes are different for vehicles like this one.

IE: What are some engineering challenges you’ve faced so far?
“There have been a lot. Figuring out how the battery is used has been a challenge because the design isn’t fixed. We haven’t validated how this vehicle will be used. Can we swap the batteries, or do we recharge upon landing? What kind of battery life should we expect from this type of vehicle? Determining how to optimize battery usage is a challenge.
Aerodynamically it’s a challenge. Especially with this tech demonstrator, the counter-rotating propellers cause a lot of aerodynamic interaction from propeller to propeller — a lot of wake effects — and onto the body, especially when we add things like crosswind. That’s very challenging aerodynamically.
The stability required in the algorithm that controls the speed of these motors can be difficult, then linking that to the structural design. Because obviously, the main aim is to reduce the weight because the less weight we have the further range. The design of the crossbars is very key in allowing enough rigidity to not get any vibrations from the motor because that can then create instabilities and runaways that can cause problems. So, there’s a lot of tuning that’s happening. Not so much of the design is fixed yet. Everything’s been tuned at the same time.”
He stated that the team looked at octocopter designs, but they are adding more propellers, and increasing the footprint.