The surge of 3D printing has sparked innovation across industries, yet its environmental implications present formidable challenges. As the technology gains traction, a significant proportion of plastics used in printing resist easy recycling. Furthermore, the uptake of sustainable alternatives encounters hurdles due to the manual calibration required for each material, a cumbersome process hindering widespread adoption.
In response to these pressing concerns, a collaborative endeavor led by researchers from MIT’s Center for Bits and Atoms (CBA), the U.S. National Institute of Standards and Technology (NIST), and Greece’s National Center for Scientific Research (Demokritos) has yielded a game-changing solution. They’ve engineered a 3D printer endowed with the remarkable capability to autonomously discern the parameters of unknown materials, fundamentally reshaping the printing landscape.
Central to this innovation is the modification of the printer’s extruder, the critical component responsible for material deposition. Equipped with sensors capable of measuring material forces and flow dynamics during a succinct 20-minute test, the research team extracts vital data.
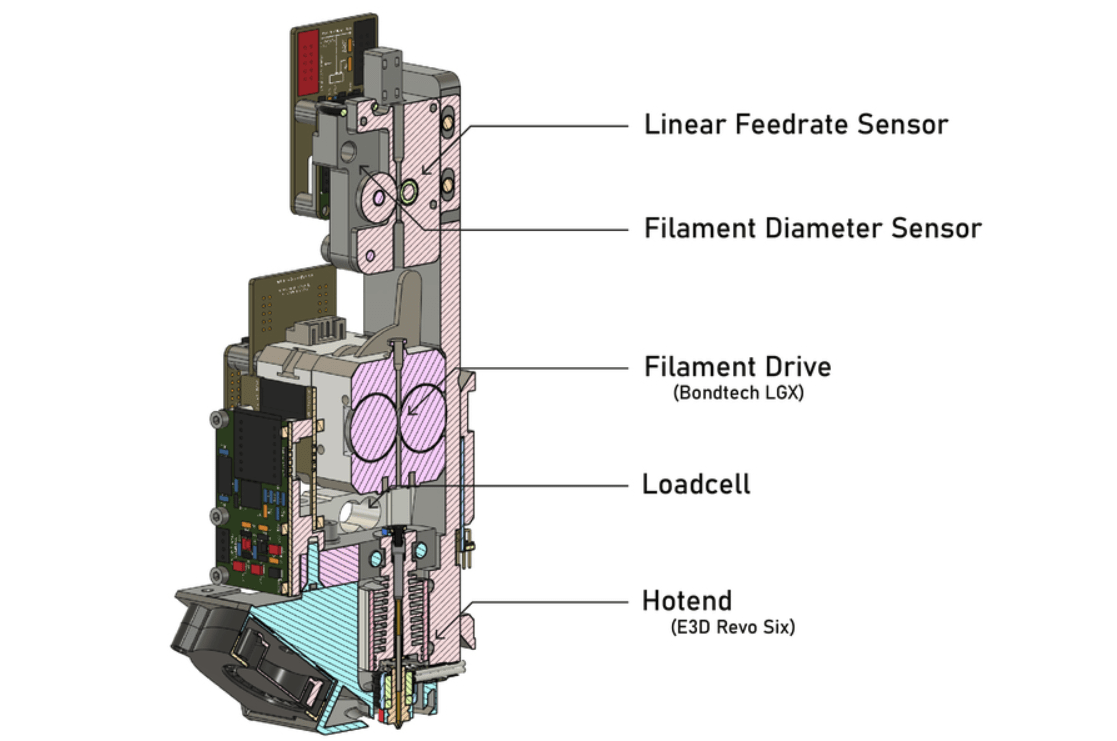
This data fuels a sophisticated mathematical model that ingeniously generates printing parameters automatically, obviating the need for laborious manual adjustments and facilitating the seamless integration of novel materials into the printing process.
“In this paper, we demonstrate a method that can take all these interesting materials that are bio-based and made from various sustainable sources and show that the printer can figure out by itself how to print those materials. The goal is to make 3D printing more sustainable,” says senior author Neil Gershenfeld, who leads CBA.
The implications of this breakthrough are profound. Significantly, the automatically generated parameters have the potential to supplant up to half of those traditionally calibrated by hand, streamlining the printing process substantially. Through a rigorous series of test prints using various renewable materials, the researchers have underscored the consistency and viability of their method, highlighting its transformative potential.

This research carries the potential to significantly decrease the environmental impact of additive manufacturing. By facilitating the adoption of sustainable materials in 3D printing, it offers opportunities to enhance the industry’s ecological standing. Neil Gershenfeld, the principal investigator of the study, envisions a future where 3D printing embraces bio-based and recycled materials, thus nurturing a more sustainable manufacturing landscape.
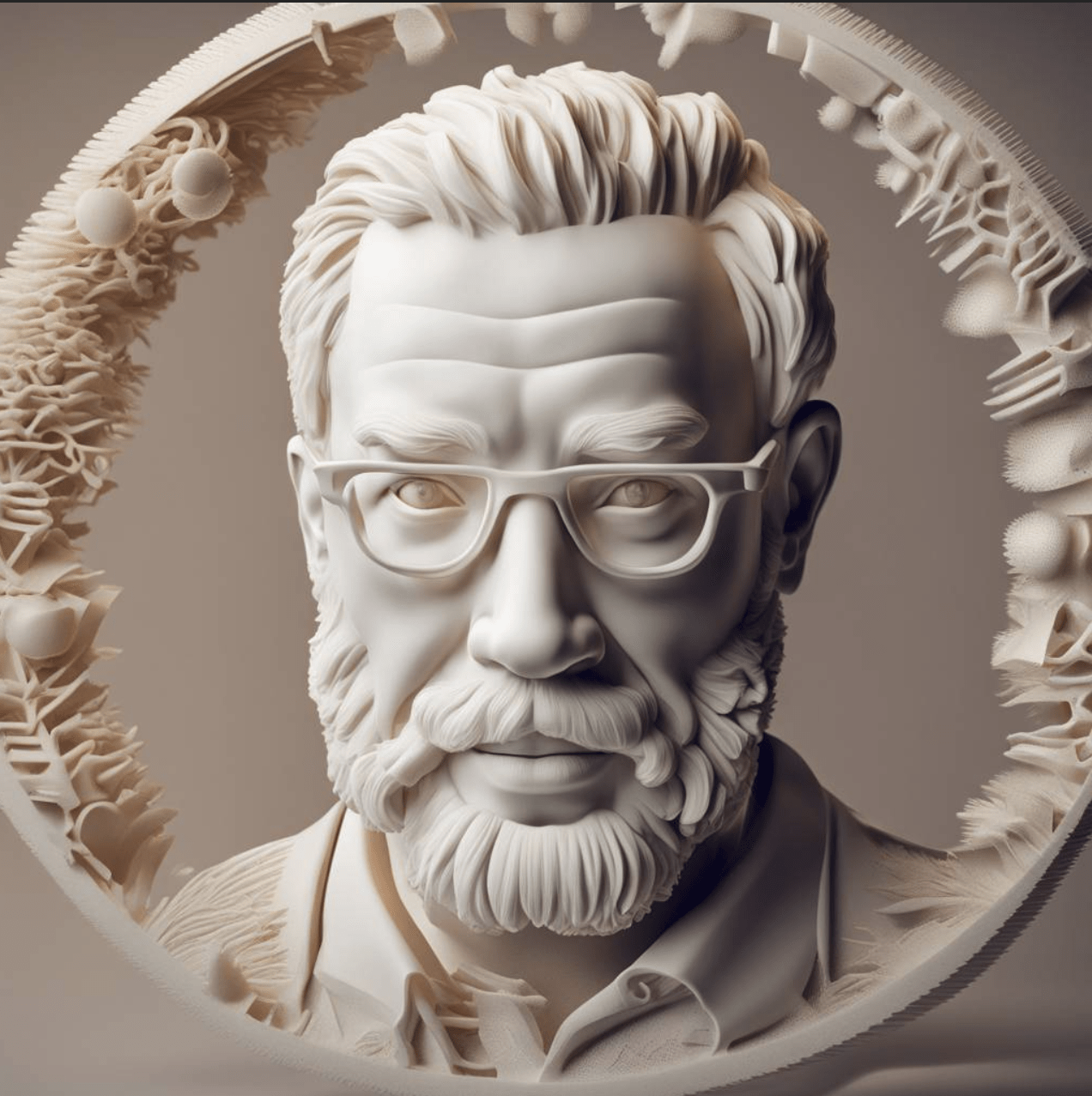
Underpinned by the collaborative endeavors of Gershenfeld and his team, this pioneering research signifies a critical juncture in the evolution of 3D printing. Not only does it tackle urgent sustainability issues, but it also underscores the transformative capabilities of autonomous systems in manufacturing. Through the automation of parameter generation, this study not only simplifies the printing process but also heralds a fundamental shift towards a greener, more sustainable future in manufacturing.
“By developing a new method for the automatic generation of process parameters for fused filament fabrication, this study opens the door to the use of recycled and bio-based filaments that have variable and unknown behaviors. Importantly, this enhances the potential for digital manufacturing technology to utilize locally sourced sustainable materials,” says Alysia Garmulewicz, an associate professor in the Faculty of Administration and Economics at the University of Santiago in Chile who was not involved with this work.
The research is published in the journal Integrating Materials and Manufacturing Innovation.