A 100-person all-electric plane could be available by 2026, significantly shortening the timeline for the introduction of a non-kerosene-powered commercial airliner.
U.S. startup Wright Electric Inc. intends to retrofit electric motors into a BAe-146 regional aircraft initially manufactured by BAE Systems Plc, replacing its four jet engines and converting it into a zero-emissions model.
The 1,000-kilometer (620-mile) flight between Sydney and Melbourne, London-Geneva, Tokyo-Osaka, or Los Angeles-San Francisco will be handled by Wright’s initiative, which will use high-density energy storage. Once in production, the Wright Spirit, based on the BAE 146, will primarily be a 100-seat electric alternative used on various popular flight routes.
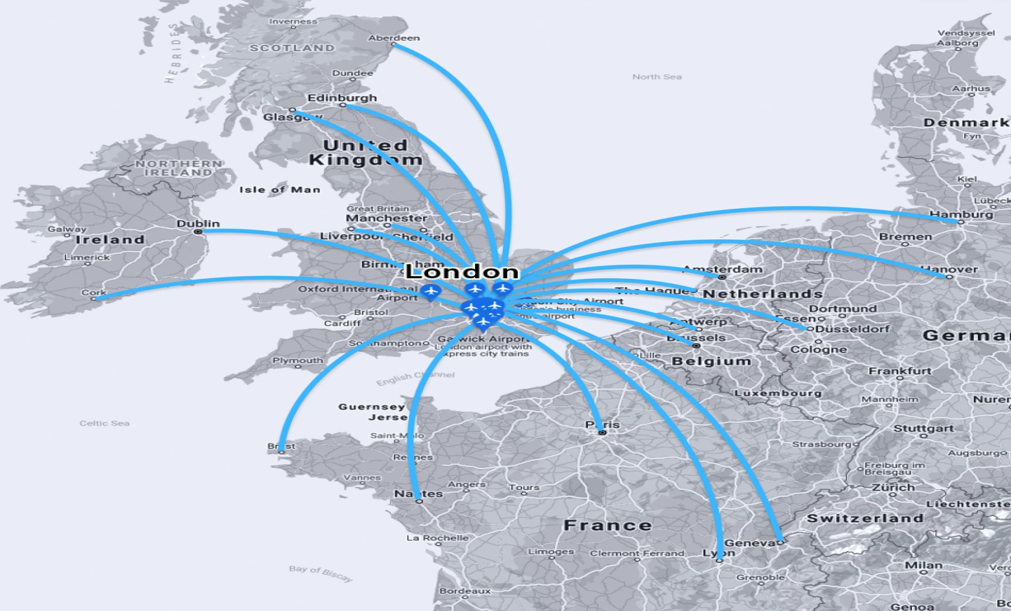
Wright’s plan does rely on advances in battery technology, the CEO said, with the retrofit model requiring slightly bigger motors than the two-megawatt system it’s currently testing. Hydrogen fuel cells or aluminum fuel cells could deliver the necessary 2.5MW to 3MW capacity.
But, unlike most airliner initiatives, why isn’t the company opting for hydrogen? Volume is one of the most important factors. Liquid hydrogen is an excellent lightweight energy storage medium in terms of weight. The majority of these early projects will be upgrade kits for airframes that were not designed to handle the additional volume of hydrogen because the volume is valuable to commercial aircraft operators.
In contrast, aluminum does not carry as much energy by weight as jet fuel or liquid hydrogen. With a carbon cathode and catalysts buried behind a porous polymer separator, it serves as an anode. Between the two is an electrolyte, an essential liquid. The aluminum and atmospheric oxygen react at the cathode to form a hydrated aluminum oxide that releases energy. Since the cathode and electrolyte add weight to the system, the specific energy ceiling of aluminum is reduced to 60-70 percent.
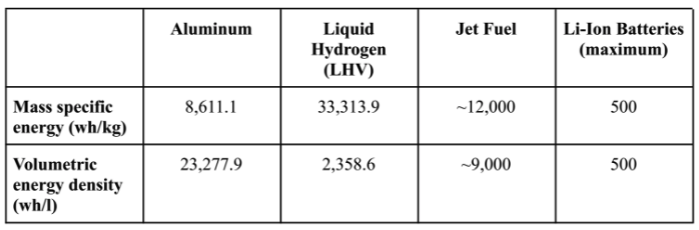
However, Wright claims that “since half of the single-aisle market is flights shorter than 800 miles (1,287 km), the range penalty might not be as consequential as it might initially seem.”
To avoid any misunderstandings, Wright refers to it as a fuel cell instead of an aluminum-air battery. This is because it needs to be refueled like a fuel cell does, but it also has to collect aluminum oxide deposits for recycling.
This, according to Wright, will be less difficult than coming to grips with liquid hydrogen tanks. While the hydrogen infrastructure is still being constructed, aluminum smelters worldwide can recycle aluminum oxide into new metal in planes or other applications. It would be quite simple; canisters can be transported in trucks and loaded onto planes like cargo. If the metal is in pellet form, it can be sent down pipes if necessary.
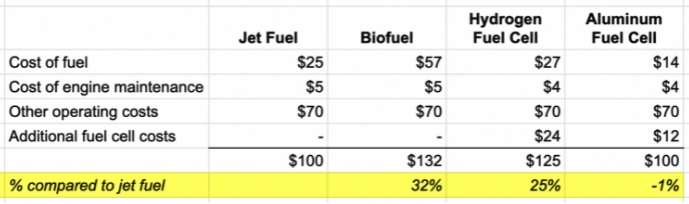
However, the thin, cold, low-oxygen air at cruise altitudes necessitates compressors and heat exchangers, putting the weight budget at risk. As a result, more aluminum would need to be exposed for higher reaction rates, which could be attained using powders or pellets instead of plates. Thus, there is still work to be done.
Wright estimates that the aluminum system would be cheaper than today’s jet fuel operations since hydrogen fuel cells are expected to increase costs by around 25% and biofuels by about 32%.
At this moment in time, Wright is impartial, highlighting the hydrogen vs. aluminum debate as follows:
“Hydrogen fuel cell: longer range, smaller payload, harder operations, higher cost.
Aluminum fuel cell: shorter range, larger payload, easier operations, lower cost.”
Source: Wright Electric