There is a new “Greenaxe” electric guitar by Olaf Diegel that is made by an innovative 3D printing technique that turns waste products like sawdust into high-strength, production-grade wood parts.
Forust is the company that introduced this technique. The company was recently acquired by Desktop Metal. The mechanism involves the use of waste sawdust and lignin that have no real uses. They are used as a powder feedstock in a binder jetting process. Different densities can be achieved with different strength and weight characteristics. Also, the finishing can be of mimicked woodgrain or without.
Diegel, a Professor of Additive Manufacturing at the University of Auckland, has ample experience with 3D-printed guitars through his ODD Guitars business. It was him who brought the clockwork steampunk axe to the market.
The Greenaxe is going to be his first wood-printed guitar. He was commissioned by Desktop Metal so the company could exhibit what it is capable of achieving after the acquisition. The design clearly screams, “look how 3D printed I am,” and it has some more intriguing features as well.
It is made up of wood and experts state that wooden instruments sound better over time as they constantly undergo harmonic vibrations that allow its molecules to align toward the parts that vibrate the least, leaving slightly less material at the points that vibrate the most, much like those sand on a speaker tests. In this hypothesis, the lightening of the fastest-vibrating parts of the instrument body would potentially help them become more resonant and responsive.
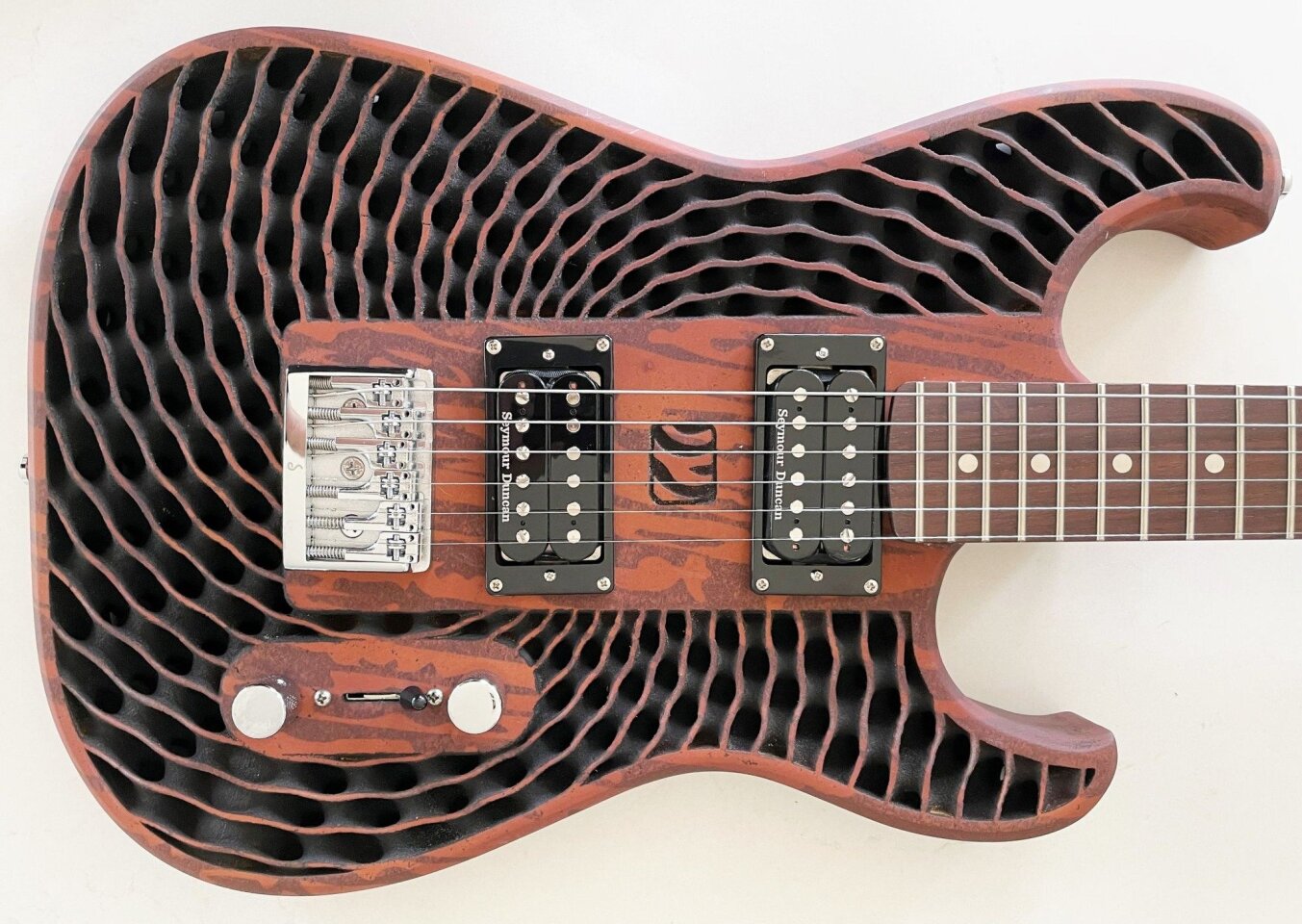
If this is proved correct in practicality, wooden guitars designed like this can be more successful than anticipated. Also, the bodies of guitars and violins can be designed from wood, so they have better output. It will enhance the key frequencies, using acoustic modeling or even by measuring test vibrations and tracking where they tend to resonate through a solid wood body.