As we know, cement is the main component that is utilized in the construction process, but have you ever wondered how dangerous it is for the green environment in terms of greenhouse emissions? Researchers at Flinders University have now optimized the concept of recycling industrial waste by passing it through an incredible transformation. They transfigured a new type of polymer that can be used for building bricks and is a major breakthrough in the construction industry. The most interesting thing to note is that this polymer does not need any mortar or adhesives as it has a tenacious ability to stick around effectively.
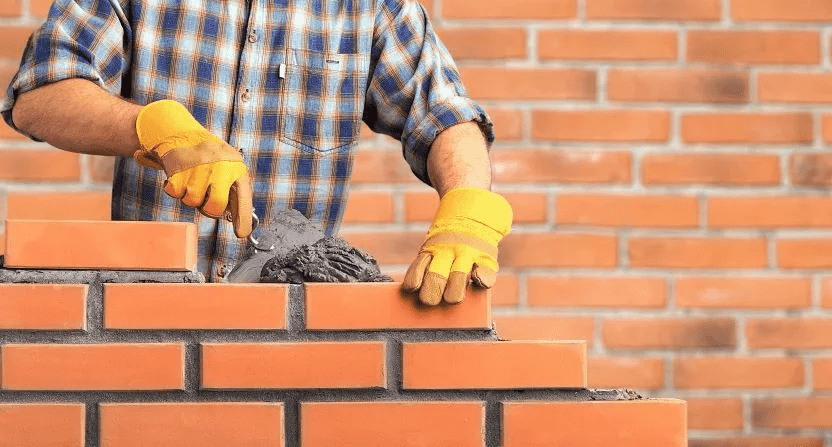
It should be noted that the polymer has been made out of industrial waste products and has been developed through an entire recycling process. As a matter of fact, cement contributes 8% of the carbon dioxide emissions, and discovering such materials which can mitigate the carbon footprint on the environment is the need of the hour. On that count, wood or old tires have been widely used in transforming the construction process and keeping the environment safe. Sulfur (waste from industrial processes) has been added to the current polymer in the initial stages of the process to make it more sustainable.
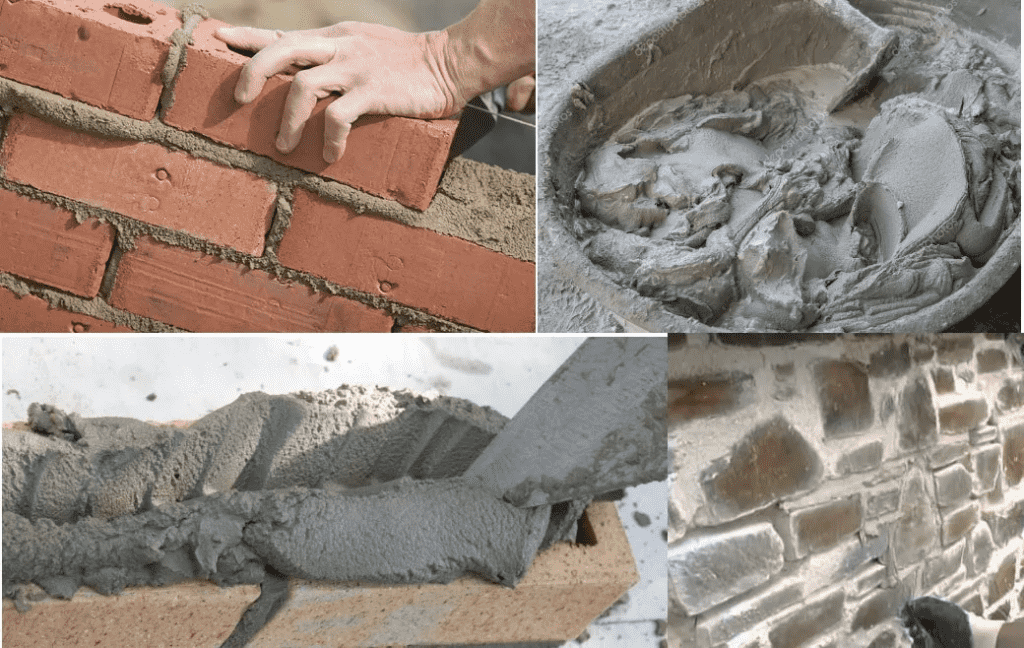
As of now, the polymer has been made from canola oil and dicyclopentadiene (DCPD) along with sulfur. Canola oil is taken from kitchen waste. However, sulfur and DCPD usually come as waste materials from the petroleum refining industry. These three elements would then be heated and metamorphized into the form of bricks which would then be used for construction purposes. Technically, the process is more viable and sustainable than cement production.
Professor Justin Chalker, who is the author of the study, said, “An amine catalyst is sprayed onto the surface. The catalyst causes the S-S (sulfur-sulfur) bonds in the brick to rearrange and bind the two bricks together. The catalyst only needs to initiate the reaction, and it evaporates from the bricks after bonding. ” Different tests have been conducted on these polymer bricks so far, and it has been found that the bricks are more efficient, lightweight, and resistant to bad weather conditions as compared to conventional bricks.
The researchers added carbon fiber to these bricks by the researchers to assure their strength, and it came out that they are 16 times stronger. Moreover, the team has been making efforts with the coordination of “Clean Earth Technologies” to commercialize the process and bring it into practical use.