Some of the strongest materials to build with are titanium alloys but they are not only expensive but heavy as well. Researchers at the University of Maryland (UMD) have used a new densification process to make super wood that has the same strength and toughness as steel.
Wood is probably the most used construction material already and the UMD team is working to make it even more useful. Liangbing Hu is leading the team responsible for developing the super wood. The researchers first boil samples of wood in a watery mixture of sodium hydroxide and sodium sulfite, which partially removes lignin and hemicellulose from the material. This wood is then hot-pressed causing the cell walls to collapse and form highly-aligned cellulose nanofibers. This gives rise to densified wood, which is stronger than natural wood.
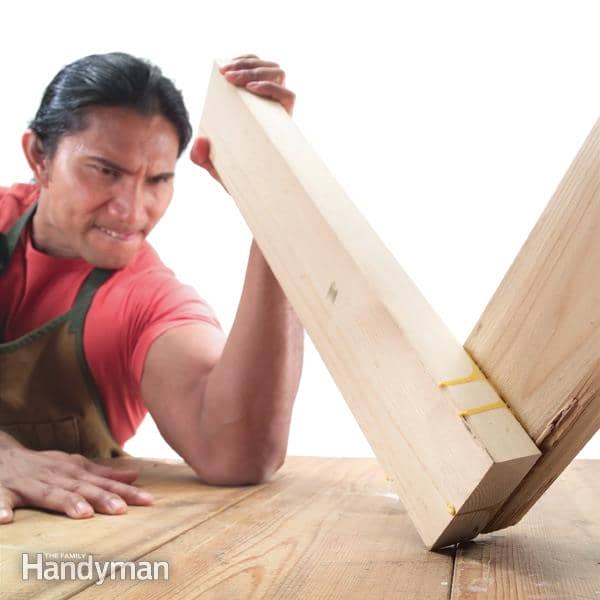
“This new way to treat wood makes it 12 times stronger than natural wood and 10 times tougher,” says Hu. “This could be a competitor to steel or even titanium alloys, it is so strong and durable. It’s also comparable to carbon fibre, but much less expensive.”
The team fired projectiles at the wood to test it. The projectiles blasted right through the natural wood but the super wood was able to stop the projectiles partway through. According to the researchers, this process can be applied to many different kinds of wood and can be scaled on an industrial scale to treat large amounts at once. The wood can be bent and moulded into any desired shape at the beginning of the process.
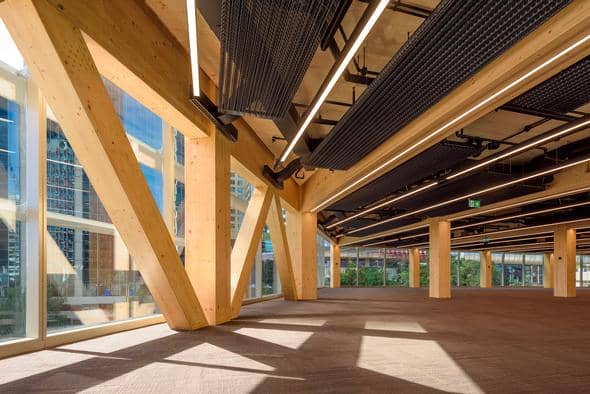
“This kind of wood could be used in cars, aeroplanes, buildings – any application where steel is used,” says Hu. “Softwoods like pine or balsa, which grow fast and are more environmentally friendly, could replace slower-growing but denser woods like teak in furniture or buildings.”
Using this technique can allow wood to be used in the place of steel in some cases and will open many new doors for cheaper construction.