The batteries are a crucial part of this system and they had to consider a number of factors including the power to weight ratio and life of battery. The modeling they did in FLOPS gave them specifics for the battery they needed. Accordingly they needed energy enough to provide them with a thrust of more than 6,000 lbs at a speed of 368 km/hr. This came down to be 1500 kW per engine. Their final choice of battery was a Lithium polymer battery which ended in a total weight of batteries equaling less than 13,000 lbs.
NASA Tests A Hybrid Plane That Works Like A Toyota Prius
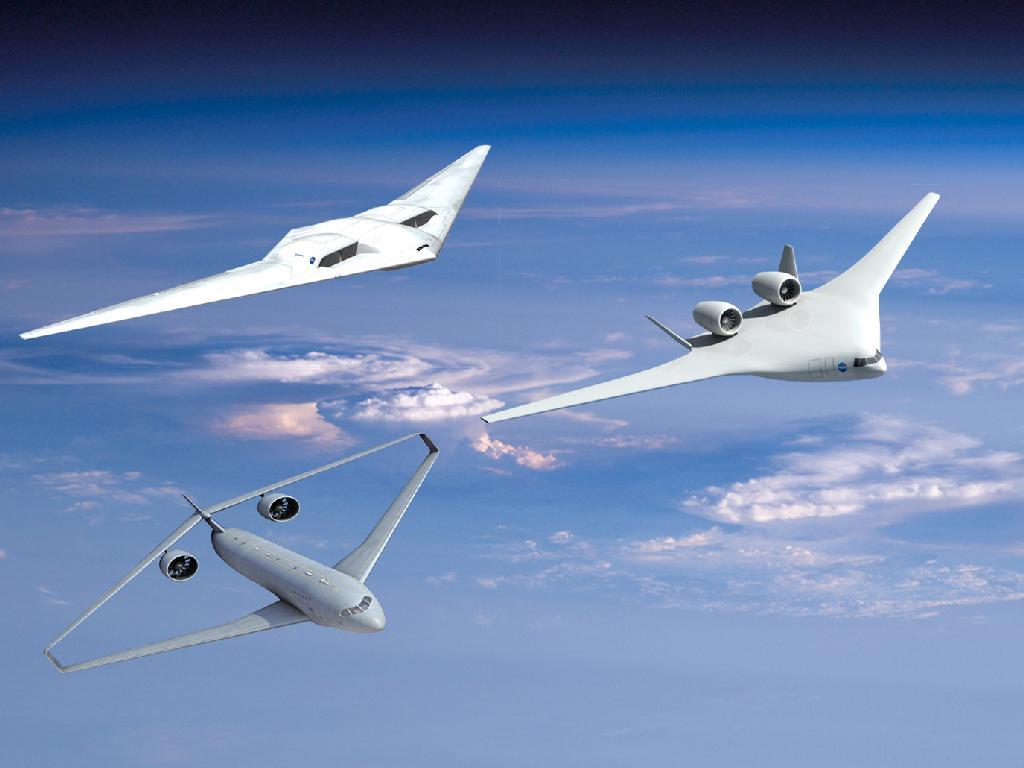