Whether it’s providing emergency shelter after a natural disaster or supporting military operations in austere environments, rapidly deployable shelters play a vital role. As missions become more complex, the requirements for these portable shelters are evolving. Advanced materials, smarter designs, and modular components are shaping the future of deployable shelter systems.
The pace of innovation is accelerating to meet the dynamic challenges of both temporary humanitarian housing and tactical field operations. Leaders must keep up with the latest trends as they evaluate options and plan deployments. Understanding where technology is headed will ensure you select the most capable and flexible shelter systems now and into the future.
Lightweight Strength
Since portable shelters need to be transported and set up quickly, weight is a key consideration. New high-strength fabrics and plastics are enabling significant weight reductions without compromising durability. For example, thermoplastic olefin fabrics provide a robust external skin that withstands harsh weather, resists puncture, and weighs up to 50% less than traditional canvas coverings.
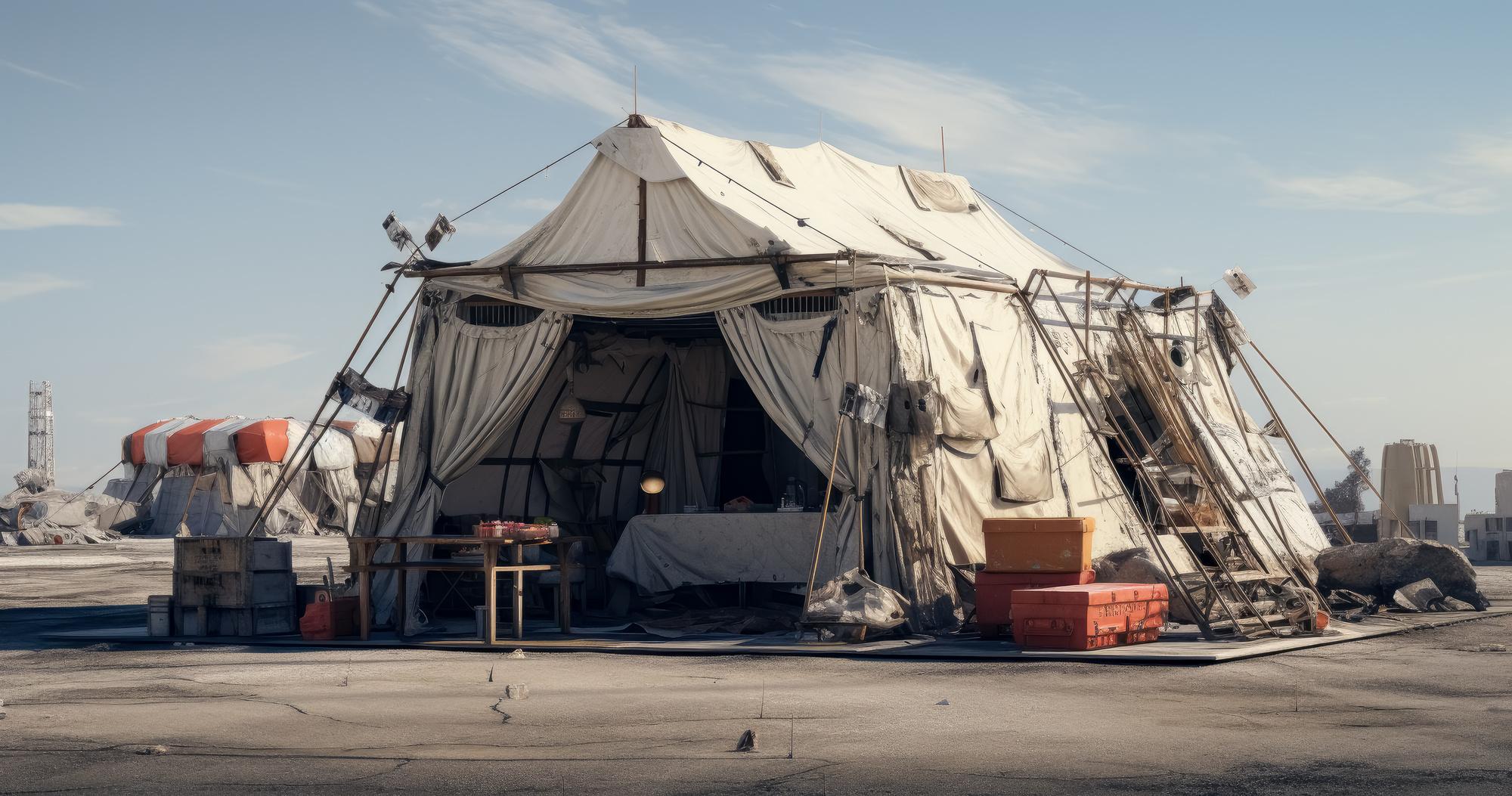
Interior rigid framing is also moving to lighter materials. Aluminum space frames can now match the strength of steel at one-third the weight. Composite material trusses combine carbon fiber and fiberglass in rigid beams that are even stronger by weight than aluminum. As framing gets lighter, larger shelters can be relocated or airlifted by helicopter to operate further forward in more austere environments.
Hybrid Design Flexibility
The combination of soft and rigid elements is allowing innovative deployable military shelter systems designs. Fabric structures provide rapid setup and tear down plus easy transport. Interlocking rigid framing lends stability and allows larger spans. Putting these technologies together in hybrid shelters brings out the best of both approaches.
Some modern shelters use composite arch frameworks overlaid with insulated fabric panels. The arches deploy in minutes without tools to create a robust structure able to cover even up to 1,600 square feet while the whole unit packs into a compact container for transport. The possibilities of hybrid designs are just starting to be explored and provide versatile options for field use.
Climate Improvements
Whether it’s sweltering heat or frigid cold, the climate inside a shelter dramatically affects functionality. The latest materials and technologies are making deployable shelters more livable across diverse environments.
Advancements like triple-layer insulated roofing and foam core panel walls better regulate interior temperatures. New polymers reflect more sunlight to reduce heat gain. Improved rain gutters and seals prevent leaks, while cove bases manage runoff and mitigate flooding. Heating and air conditioning units have become more efficient and flexible for off-grid power generation
Making shelters more comfortable also improves morale and productivity for those inside, be they first responders after a disaster or soldiers maintaining readiness.
Modular Power Networks
Reliable power is essential for sustained operations within a shelter. Modular electrical distribution systems enable adaptable delivery of electricity. Components like cabling, junction boxes, and outlets interconnect without tools to form plug-and-play power networks in various configurations.
Standardized power connections allow quick expansion, like adding another shelter module. Generator integration and solar panels provide off-grid capability. Segmenting the power system across multiple smaller distributors prevents single-point failures.
Modular power technology combined with energy storage gives deployable shelters robust standalone energy infrastructure to support their mission.
Interoperable Connections
Innovations in connections are making shelters easier to assemble, reconfigure, and combine. Key interoperability standards are emerging across vendors to allow greater component compatibility.
Universal Power Distribution Units (UPDU) enable all electrical fixtures to plug into a single power grid. Standard camlocks rapidly connect shelters and make swapping panels simple. Interlacing poles that lock with spring-loaded buttons allow tool-free assembly of framing.
Common connection types mean shelters can be put together in more arrangements with reduced specialized labor. Parts are interchangeable across vendors. Hardware innovations are streamlining construction and enhancing flexibility.
Automated Deployments
To further increase the speed of getting a shelter operational, automation is being built into more models. Hydraulics systems allow shelters to be set up with the push of a button instead of manual labor. Walls and roofing unfold, extend, and lock into place mechanically.
Inflatable shelters provide rapid one-step deployment as air beams spontaneously expand and rigidize when inflated. Some systems like Alaska Structures’ SECRA inflatable even pack down small enough for air transport on helicopters. Automation reduces manpower needs and enables shelters to be operational in hours instead of days.
Durable Materials
Once erected, shelters must withstand punishing conditions from freezing cold to sandy gales. Their ability to maintain integrity keeps personnel and assets protected. Rugged fabrics purpose-engineered for shelter exteriors resist punctures, UV damage, and tearing.
Coated ripstop polyesters and lightweight polymer films provide high tensile strength and durability. The latest flexible composites take resilience even further. For example, Deployable Composite Solutions make a carbon fiber composite shelter resistant to 125 mph winds and extreme weather variability.
Mold and mildew-resistant finishes help maintain interior environments in hot, humid climates. Durable shelters extend mission capabilities while reducing losses.
Larger Capacity
From command centers to surgical suites to refugee housing, portable shelters must now accommodate more people and functions. Expandable designs allow capacity to be right-sized. Modular components scale up interiors for larger-scale operations and to bring more functionality undercover.
Hard-wall containers used as sleeping quarters or offices can be stacked two levels high and linked together. Soft-walled tents or inflatable shelters are expandable to over 5,000 square feet. Larger yet relocatable shelters allow a small initial footprint to become a medium-scale installation.
Expanding capacity enables a single site to support more operations, personnel, and services – a must for complex deployments.
Enhanced Modularity
Interchangeable components from different vendors increase flexibility for planners. With standardized connections, shelters have fewer proprietary elements and more plug-and-play modularity.
Joints like a hub connector work across manufacturers to interface frames, panels, and accessories. Electrical plugs adapt across brands, simplifying power distribution. Swappable fixtures and options let you select from more suppliers to optimize cost and performance.
Greater modularity gives planners more flexibility, combining elements from their inventory into customized solutions. It reduces vendor lock-in and improves interoperability across platforms.
Final Thoughts
The future favors adaptable systems over static solutions. Planners should look for open architectures that integrate advances while avoiding proprietary lock-in. Investments made today will be used in unforeseen ways tomorrow, from disaster recovery at home to expeditionary operations abroad.
But technical advances must be balanced with human needs. The most capable shelters will fuse both, empowering people to more safely and effectively achieve objectives. With flexibility as a guiding principle, deployable shelters are poised to provide that progressive foundation for defense operations now and into the future.