The International Space Station (ISS) has seen the completion of the first-ever metal 3D printing project by a group led by Airbus, marking an incredible milestone.
The successful printing of a tiny S-shaped curve made of liquid stainless steel took place on May 30. This test line shows that the printer could soon begin creating functional materials, according to the European Space Agency (ESA). According to ESA technical officer Rob Postema, “the success of this first print, along with other reference lines, leaves us ready to print full parts in the near future.”
According to ESA, in the future, parts from abandoned satellites could be recycled by 3D printers on board the International Space Station (ISS), promoting a circular economy in space.
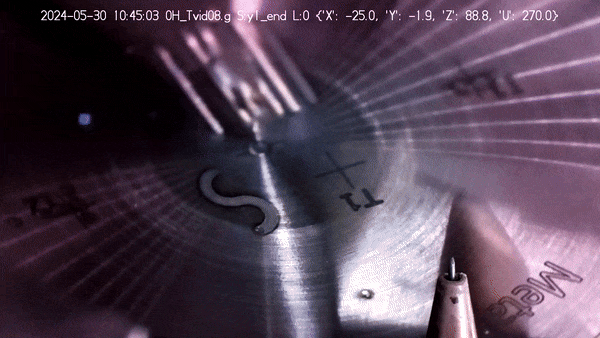
The metal 3D printer, weighing approximately 180 kg (396 lbs), was transported to the ISS on January 30 via the Cygnus NG-20 mission, launched by a SpaceX Falcon 9 rocket. Although plastic-based 3D printers are already in use on the ISS, metal 3D printing presents additional challenges due to the need for high-temperature lasers to liquefy the metal. To address this, the metal printer is enclosed in a fully sealed box to prevent excess heat and fumes from escaping.
The metal printer’s successful operation is attributed to the concerted efforts of the industrial team led by Airbus Defence and Space SAS, the CADMOS User Support Centre in France, and ESA’s team. “We’re very happy to have performed the very first metal 3D printing aboard the ISS,” commented Sébastien Girault from Airbus. The quality is as good as we could dream!”
ESA astronaut Andreas Mogensen installed the printer in the Columbus ISS module. The process involves feeding stainless-steel wire into a chamber, which is then heated by a high-power laser, melting the steel and enabling it to be shaped by the printer. The entire operation is controlled from the ground, with the ISS crew only needing to open a nitrogen and venting valve before the test.
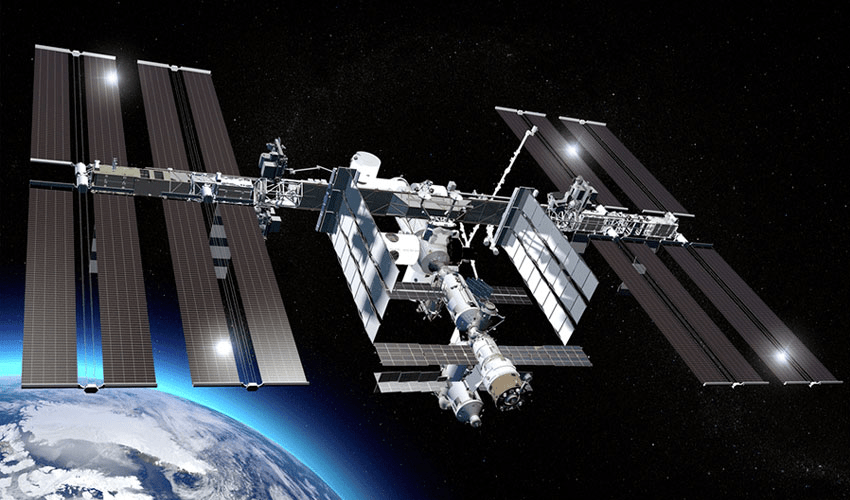
Printing four shapes that will be sent to Earth for analysis is the next step. “Two of these printed parts will be analyzed in the Materials and Electrical Components Laboratory at ESTEC in the Netherlands to help us understand whether prolonged microgravity affects the printing of metallic materials,” explained ESA materials engineer Advenit Makaya.
“The other two will go to the European Astronaut Centre and the Technical University of Denmark, DTU.”