Concrete and steel production are significant contributors to global CO2 emissions, but a groundbreaking solution from Cambridge offers a promising way to recycle both materials simultaneously, potentially leading to entirely carbon-zero cement. Concrete, the most widely used building material globally, is notoriously environmentally unfriendly, responsible for approximately 8% of total CO2 emissions. Recycling old concrete into a form suitable for new structures has posed challenges, prompting scientists to explore greener alternatives.
In a study led by Dr. Cyrille Dunant, researchers investigated the conversion of waste concrete back into clinker, the essential component of cement. Their innovative approach involved utilizing electric arc furnaces, typically employed in steel recycling, to facilitate the process.
“I had a vague idea from previous work that if it were possible to crush old concrete, taking out the sand and stones, heating the cement would remove the water, and then it would form clinker again,” said Dr. Cyrille Dunant, first author of the study. “A bath of liquid metal would help this chemical reaction along, and an electric arc furnace, used to recycle steel, felt like a strong possibility. We had to try.”
These furnaces require a “flux” material to purify steel, traditionally lime, which is discarded after use. In the Cambridge method, recycled cement paste replaces lime as the flux. The resulting slag, when rapidly cooled, transforms into new Portland cement, maintaining similar performance to conventional concrete.
Crucially, this technique minimizes additional costs to both concrete and steel production while significantly reducing CO2 emissions compared to traditional methods. If powered by renewable energy sources, the electric arc furnace could effectively produce zero-emission cement. Initial trials in small-scale furnaces have been successful, with plans for industrial-scale trials underway. The researchers anticipate producing 66 tons of cement in two hours, with the potential to scale up to one billion tonnes by 2050.
“Producing zero emissions cement is an absolute miracle, but we’ve also got to reduce the amount of cement and concrete we use,” said Professor Julian Allwood, who led the research. “Concrete is cheap, strong and can be made almost anywhere, but we just use far too much of it. We could dramatically reduce the amount of concrete we use without any reduction in safety, but there needs to be political will to make that happen.”
“As well as being a breakthrough for the construction industry, we hope that Cambridge Electric Cement will also be a flag to help the government recognize that the opportunities for innovation on our journey to zero emissions extend far beyond the energy sector.” A patent has been filed for the process, as the first step towards commercialization.
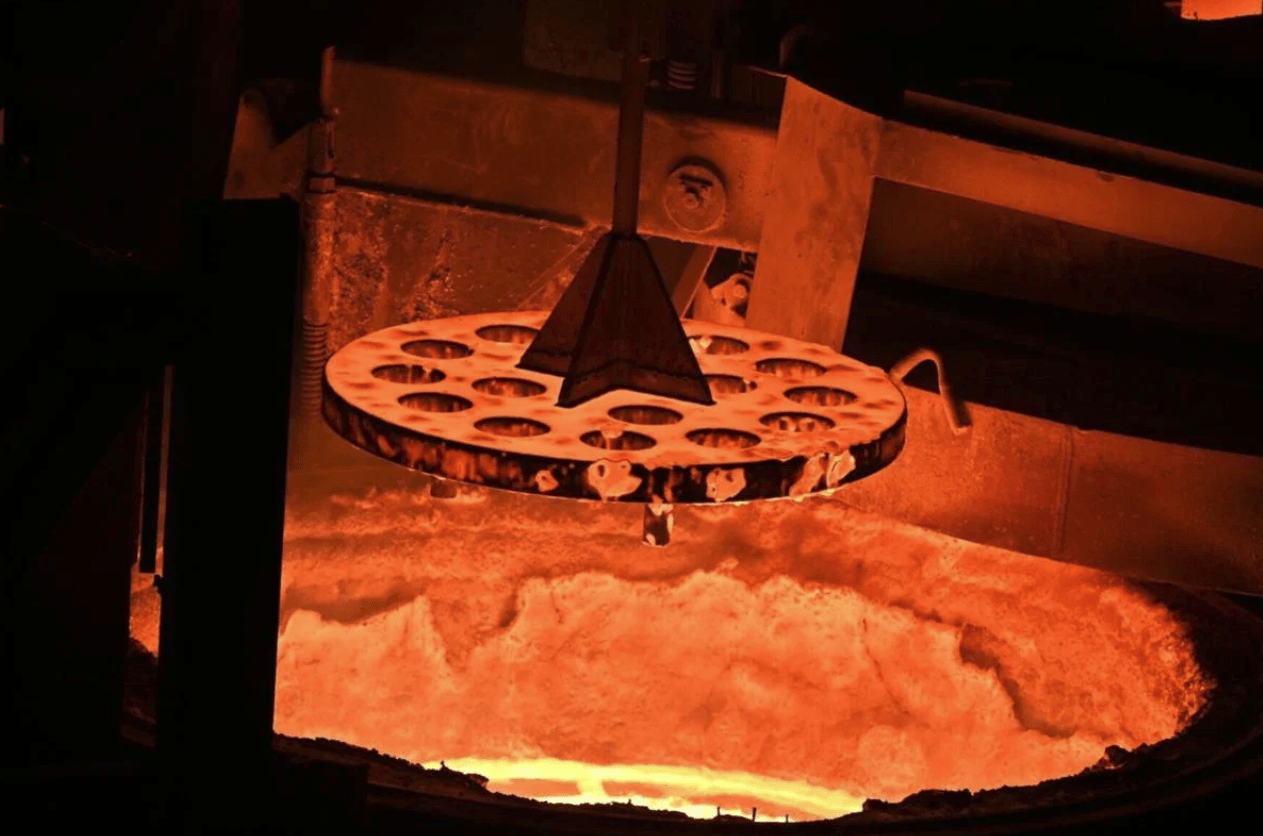
Professor Julian Allwood, who spearheaded the research, emphasizes the importance of not only producing zero-emission cement but also reducing overall concrete usage. Despite its affordability and strength, excessive concrete consumption remains a concern. Allwood highlights the need for political will to drive innovation and implement strategies for reducing concrete usage without compromising safety.
The breakthrough represented by the Cambridge Electric Cement process extends beyond the construction industry, highlighting the broader potential for innovation in achieving zero emissions outside the energy sector. Published in Nature, the research has advanced significantly towards commercialization with the filing of a patent.
By tackling the environmental impact of concrete production through recycling and sustainable practices, the Cambridge solution offers a concrete pathway towards a greener future for construction. With widespread adoption and ongoing development, zero-emission cement could become a key player in advancing global sustainability objectives and combating climate change.