Some think that getting the astronauts up into the space beyond the gravity of our planet is the most challenging part in a space mission; the truth is that getting them back down after a mission is equally difficult. The spacecraft re-entering the atmosphere are traveling at over 30,000 km/h. This outrageous speed of the re-entry vehicle turns the air below into a hot ball of fire around the craft, which means the astronauts have to be protected against thousands of degrees if they are to return home safely.
So it one of the most difficult task to design a strong enough thermal protective material for the aerospace engineers which can last at temperatures as high as 1,700-degrees Celsius.
History Of Re-Entry
Previously manned spacecraft like Mercury, Gemini, and Apollo could not be moved or steered during reentry, thus the space capsules had to follow a ballistic re-entry trajectories before plummeting into the ocean. Heat shields were usually constructed out of phenolic epoxy resins embedded in a nickel-alloy honeycomb array, which protected the capsules from the high temperatures.
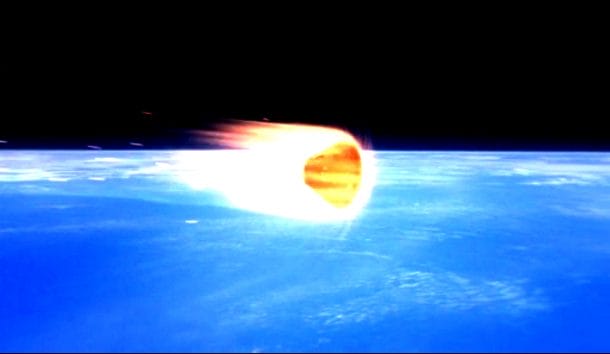
The Apollo moon mission series made the aerospace engineers rethink their designs, as the capsules returning from the moon was entering the atmosphere at more than 40,000 km/h. The previously used heatshields always caught fire, and stacking up the material made it heavy and a hindrance in its maneuverability, along with not being reusable.
Perils Of Re-Entry
One of the unfortunate accidents during a re-entry was with NASA’s first operational orbiter, Spacecraft Columbia’s return on Feb. 1, 2003. When the spacecraft was launched, a large piece of foam tore loose from the chassis and caused a fair bit of damage to a heat shield panel. This didn’t affect the mission in its entirety, but disaster struck when it was time for re-entry. The superheated plasma seeped through the broken part of the chassis and quickly burnt the structure. The Columbia went into an uncontrollable tumble, disintegrated and led to the death of seven brave astronauts.
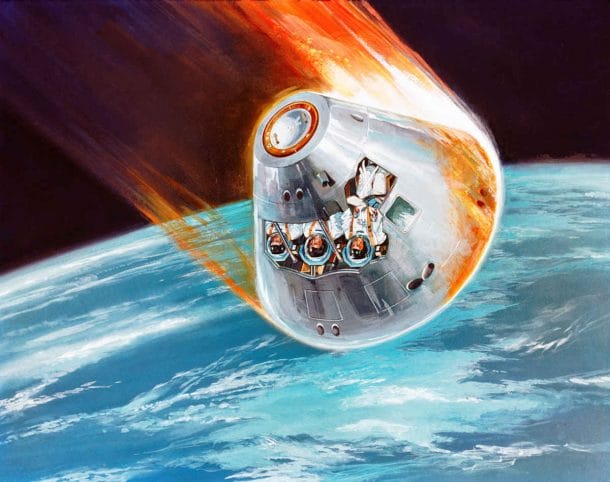
Even though the Columbia was constructed from four different materials which included reinforced carbon-carbon (RCC), low- and high-temperature reusable surface insulation tiles (LRSI and HRSI, respectively), and felt reusable surface insulation (FRSI) blankets, it went through this calamity. But NASA learned a lot from this unfortunate accident, and they changed the approach altogether for their next spacecraft, the Orbiter.
NASA learned that different parts of the aircraft must be designed for different temperatures so that the thermally resistant materials for parts of the Orbiter don’t get heated too much. As for the leading edges, they used reinforced carbon coating on the high-temperature insulation tiles. Other areas were covered with advanced flexible and reusable insulation blankets.
The outermost layer of the fuselage was covered in high emissivity coatings ensuring that helped the shuttle reflect most of the thermal heat. A mosaic of black and white tiles was created, with the white tiles helping in retaining a high thermal reflectivity and absorb minimal heat while the black tiles optimizing maximum emissivity allowing the spacecraft to lose heat quickly.
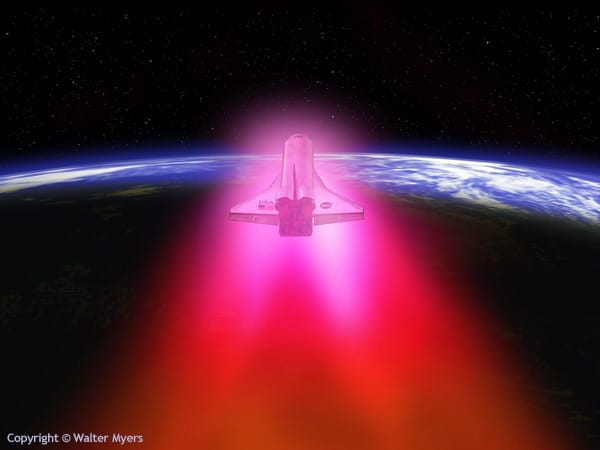
How they work
The tiles also absorb the stresses of the re-entry, and since they are made of silica aerogels, the material on the underside of the Orbiter (also known as LI-900) is essentially 94 percent of air by volume, which makes it incredibly light. The tiles can also withstand thermal shock, and the LI-900 can be heated over 1200 degrees and then crash into ice cold water without any damage. Weight of a LI-2200 tile is around 22 pounds per cubic foot bulk density, making it the perfect material to sustain the punishment.
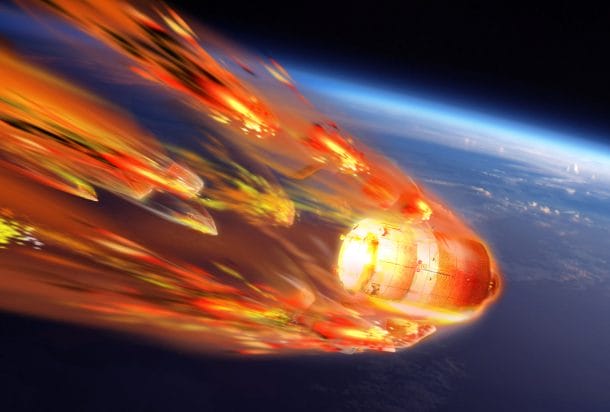
How the Orion survives Re-entry
The large surface area at the tip of the capsule takes down the blunt of the force. Orion’s heat shield is also engineered to resist high temperatures while maintaining an aerodynamically stable flight path. The design reduces the speed of the decent from 40,000 km/h to just 500 km/h.
Even that speed is further slowed down when several small parachutes over 2 meters in diameter are deployed, bringing the speed down to only 30 km/h. Then large parachutes 7-meteres in diameter are then deployed, followed by three massive main parachutes with a diameter of 35 meters, to make the landing bearable.