Due to the ever-growing demand for larger cruise ships, operators have turned to an innovative and cost-effective method known as “jumboization.”
For an average cost of around $80 million and a few months of downtime, this engineering process involves slicing a cruise ship in half, inserting a new segment, and welding it back together, allowing for an increase in capacity. This process adds new premium cabins and potentially other amenities, allowing operators to recoup their investment within a few years.
Jumboization is not a new concept; it originated after World War II, initially used to lengthen warships. Today, shipyards specialize in adding 80-130 feet (24-40 meters) to cruise ships. While the entire process can take up to nine months, the actual cutting and welding of the ship are often completed in just a few weeks.
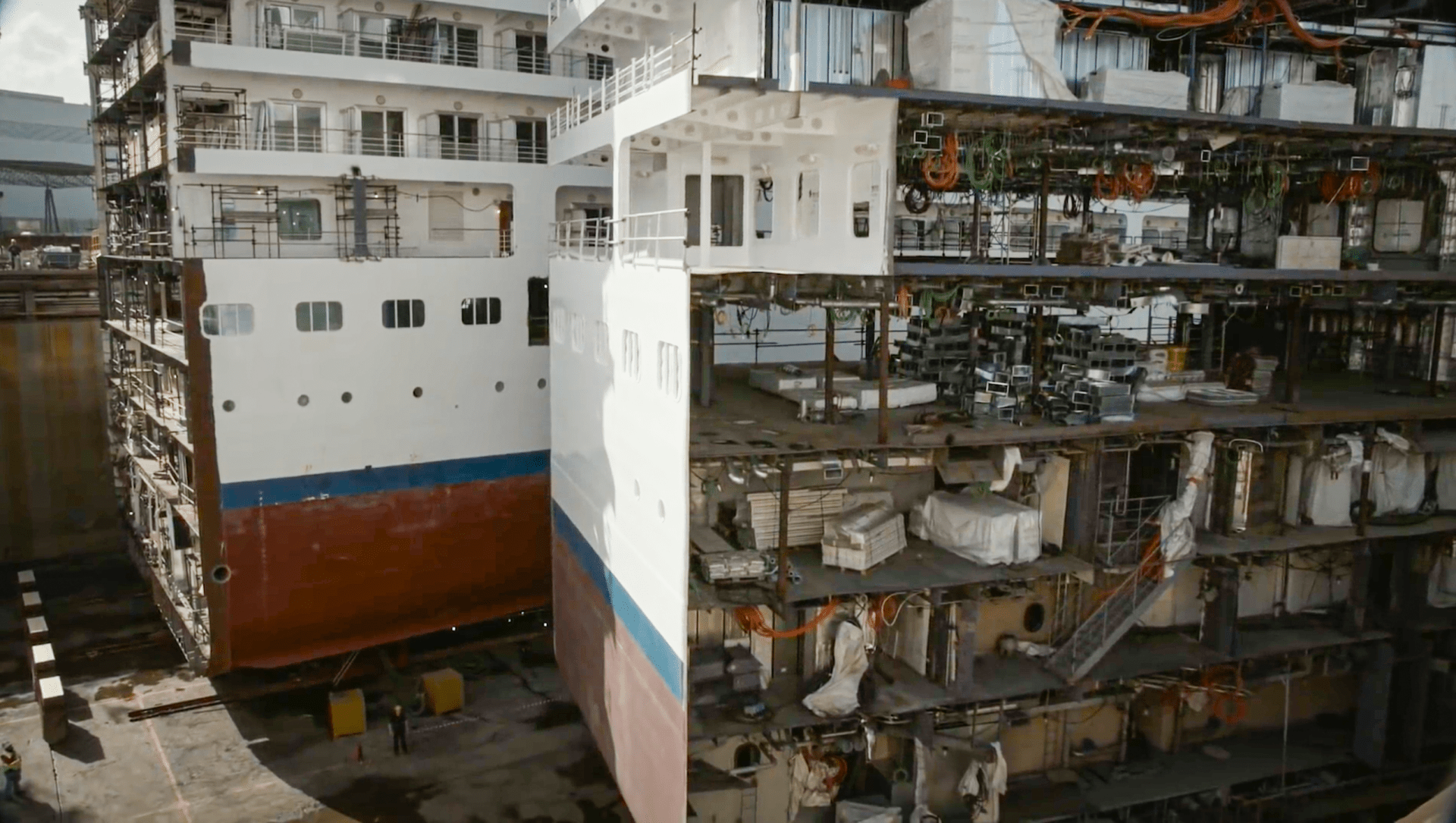
The jumboization process begins with engineers measuring and designing a new section to match the ship’s specifications. This new section is constructed, complete with interior fittings, at a shipyard. When ready, the ship is brought into a dry dock, where it is placed on hydraulic skid shoes capable of moving the vessel along metal tracks.
Once the ship is positioned, a skilled team uses laser-guided machines and acetylene blowtorches to slice through the middle of the ship with millimeter precision. The two halves are then carefully pulled apart, and the new section is slid into place, often already outfitted with furniture and fittings that would otherwise be difficult to install on board.
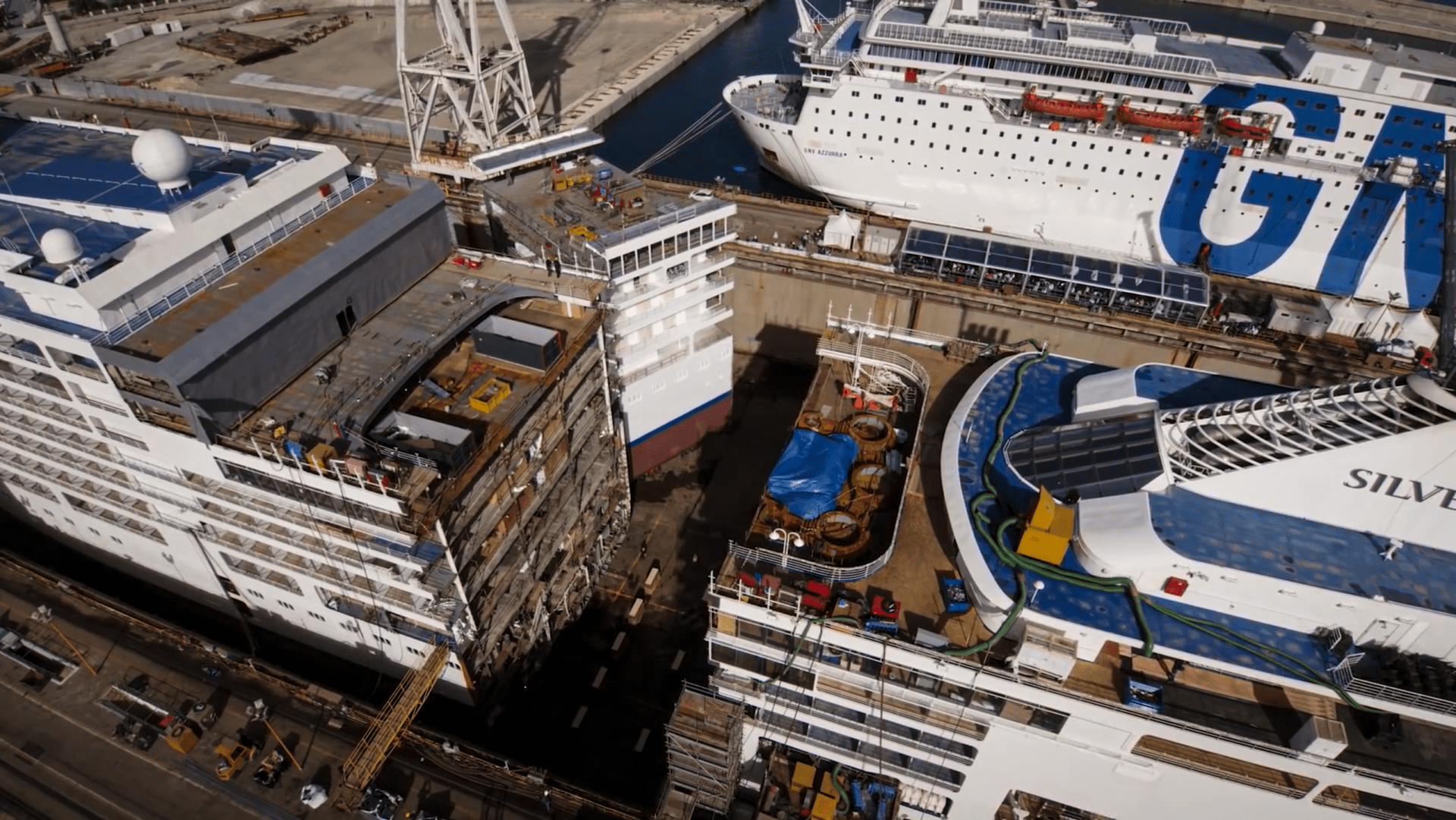
After aligning the new section, teams weld the hull and structural components together. The welds must be extremely precise to ensure the ship’s structural integrity and seaworthiness, particularly in rough seas. Electrical systems, plumbing, ventilation, and other internal components are reconnected, while the interior is renovated to make the transition seamless.
Finally, the ship undergoes extensive testing, including sea trials, to ensure all systems function properly and that the ship is ready to return to service.
One of the major advantages of jumboization is its cost-effectiveness. For significantly less than the price of building a new ship, cruise lines can increase capacity while also upgrading amenities and maintaining continuity with their existing staff.
Additionally, the process allows shipyard workers to perform other maintenance tasks, such as engine upgrades or repainting, while the vessel is out of service.
This method has proven highly successful in the cruise industry. Since 1977, at least 21 cruise ships have been lengthened through jumboization. One of the most notable examples is the Seawise Giant, the longest self-propelled ship in history, which was expanded using this technique.
Source: Spark