Mega-casting is a way for automakers to simplify the car-manufacturing process by replacing many small parts with one large metal casting.
Swedish automaker Volvo Cars has decided to invest 10 billion ($1.1 billion) Swedish Kronas (SEK) in its Torslanda manufacturing plant in Sweden to add mega-casting to its processes. This was revealed on February 8.
“The introduction of mega-casting of aluminum body parts for the next generation of electric Volvo models is the most significant and exciting change implemented as part of the investment package,” reads Volvo’s statement. “Mega casting creates a number of benefits in terms of sustainability, cost, and car performance during the cars lifetime, and Volvo Cars is one of the first carmakers to invest in this process.”
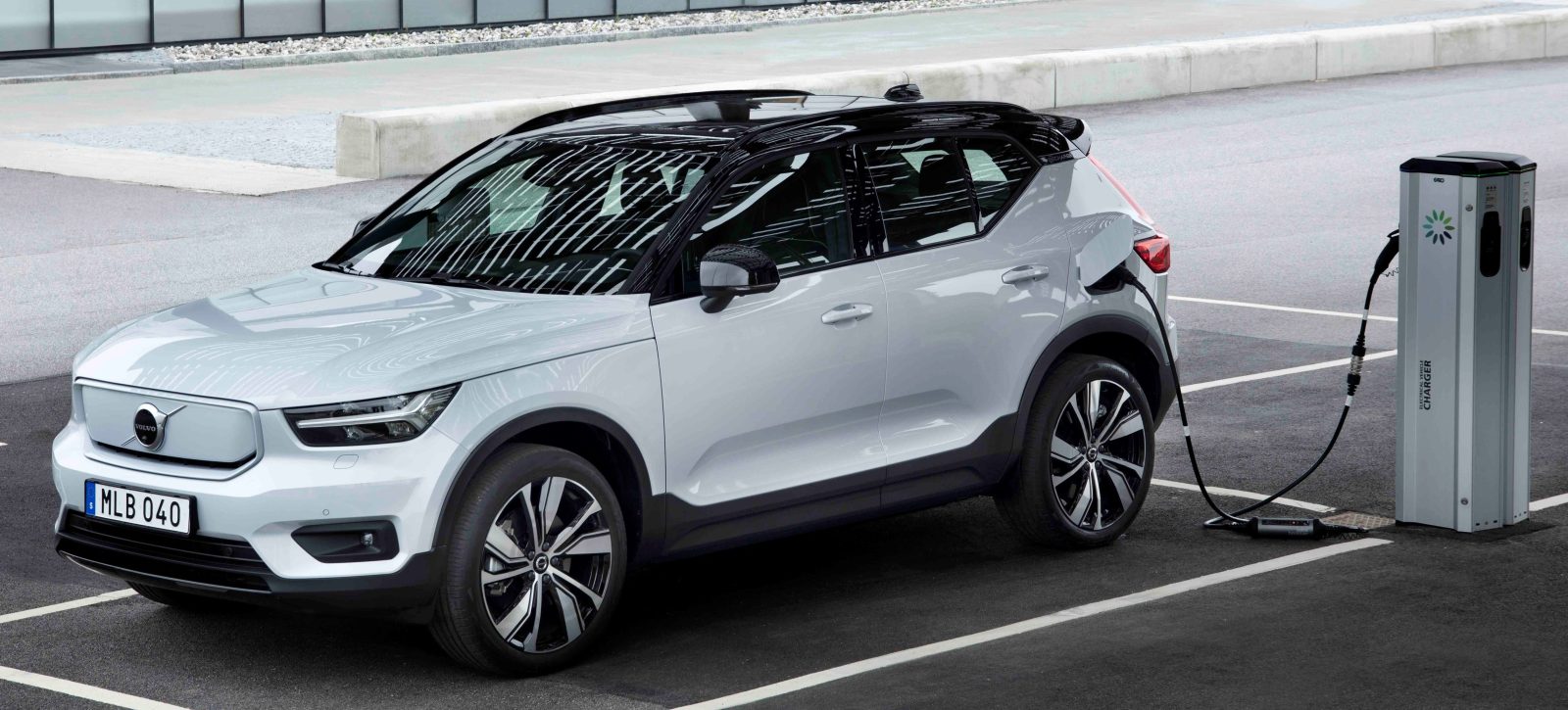
The firm believes that this investment will be well worth it because mega-casting will improve the energy efficiency along with the electric range of its cars. This will further allow vehicle designers to make the most out of the available space inside the cabin and luggage areas proving more comfort and increased space.
This will also reduce costs by optimizing material use and logistics and reducing the environmental footprint of the manufacturing process and its corresponding supply chain networks.
“Today is a great day for the Torslanda plant as we are making it fit for the future with this investment package,” said Javier Varela, head of engineering and operations at Volvo Cars. “Our future as a company is all-electric and that requires a variety of upgrades across the plant, to ensure that Torslanda can continue to build premium electric cars of the highest quality.”
Volvo Cars has also been aiming to go completely electric by 2030. In addition to investing in mega-casting, it’s also putting SEK 30 billion ($3.3 billion) in the engineering and manufacturing of high-quality tailor-made batteries specially developed for its electric vehicles.