How do turbomolecular pumps work and what are their applications? Discover the main features of these hi-tech pumps and how they help researchers and professionals in the field of high vacuum environments.
The principle of operation of a turbomolecular pump is that gas molecules can be given a momentum in a chosen direction by repeated collisions with moving solid surfaces, therefore achieving and maintaining a high vacuum region inside the pump.
A turbo pump is mainly composed of two sections: turbo and drag. The turbo section is made of alternating rotating and fixed disks containing angled blades. These are called rotors and stators, respectively.
When a gas molecule enters the inlet of the turbo pump and collides with a spinning rotor blade, the momentum imparted by the blade redirects the gas molecule further into the pump.
Gas is therefore compressed through momentum transfer: gas molecules entering the pump inlet are struck by the rotor blade and are deflected downward towards the stator blade. Multiple compression stages (Blade/Stator pairs) can compress gas to about 10-3 Torr. During each stage molecules collide with the rotor surface again and again, eventually leading them out through the pump’s exhaust.
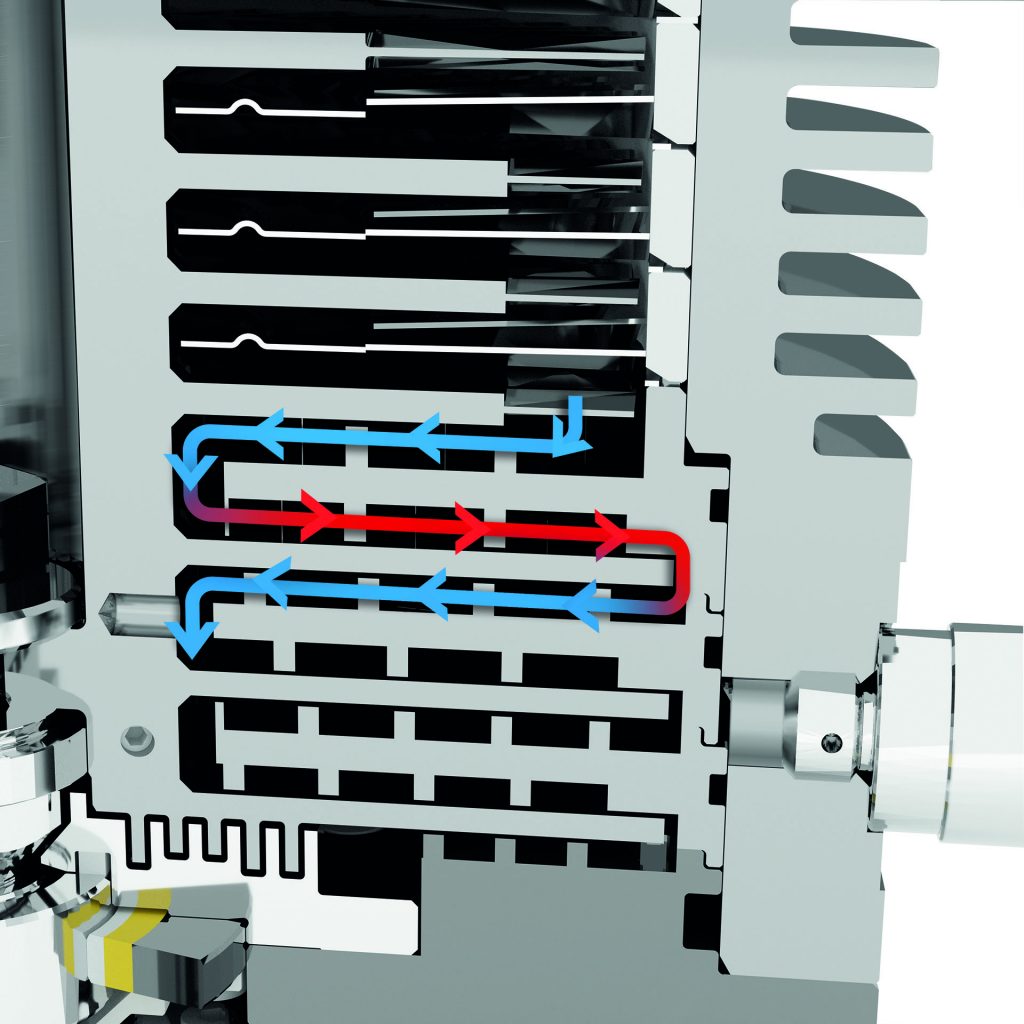
Examples of Turbo Pump Applications
Turbo-pump design has evolved in parallel with critical applications to provide optimized solutions:
The application areas involve:
- Analytical Instrumentation
Mass Spectrometry
Scanning Electron Microscope- High Gas Load/Load Lock Applications
- High-Energy Physics
Ultra-High, Ultra-Clean Vacuum
When choosing a turbo pump for a particular application, one must pay attention to performance, environmental optimization and construction quality.
For example, when dealing with high gas load applications, Agilent Technologies uses two separate approaches:
- Reduced Rotation Speed (with TwisTorr FS pump models)
- Drag Stage Selection (with TwisTorr 305-Q models)
Click here to learn more about Agilent Turbomolecular pumps
What are the ideal UHV Turbo-Pump characteristics?
- High Compression
- Ultra-clean
- No stray magnetic fields
- High Bake-out temperatures
Agilent’s TwisTorr Drag Stage design combines the benefits of Holweck and Gaede (Macro-Torr) designs:
Floating Suspension
- Proprietary bearing mounting system provides superior alignment and resistance to shocks
Grease lubricated Mechanical Bearings
- Allows ANY orientation of pump mounting
Cantilever Design
- Both upper and lower bearings are in the Rough Vacuum section of the pump
Cantilever design (vs mass central design) allows for a simpler design and also for a better radial stiffness and improved rotor alignment. Tighter radial clearances improve compression.
Agilent’s cantilever design and grease-lubricated bearings combine to produce an ideal UHV/UCV pump. Tests conducted by labs in the UK and Germany have confirmed that Agilent’s turbo design is “virtually hydrocarbon free” (on par with full mag lev turbo pumps).