In a paper published Wednesday in the peer-reviewed journal Nature, researchers presented a simple way to quantify and compare “jumpers”; whether living or non-living.
“Following these insights, we created a device that can jump over 30?[meters] high, to our knowledge far higher than previous[ly] engineered jumpers and over an order of magnitude higher than the best biological jumpers,” they write.
Their jumper, which stands just less than one foot (30 cm) high and weighs just more than one ounce (30 g), can launch itself 108 feet (33 m) into the air, with a take-off velocity of 92 feet (28 m) per second.
Jumping forces both engineers and evolution to confront some basic physical limitations of power generation. “Muscles and motors cannot generate the high-power outputs necessary to propel… jumpers on their own,” mechanical engineer Sarah Bergbreiter writes in a Perspective published alongside the paper in Nature. Living and engineered systems alike get around this limit by using their “muscles and motors to store energy in spring-like structures” before releasing the energy all once in a method called latch-mediated spring actuation, she writes.
“The rotary motors that are commonly found in engineered robots can overcome [these limitations] by acting as a winch to provide a force over a much larger displacement without needing a larger motor, thereby increasing work density,” Bergbreiter says. “As long as rotary motors can continue rotating, engineered systems are instead limited by the energy density (stored energy per mass) of the springs.”
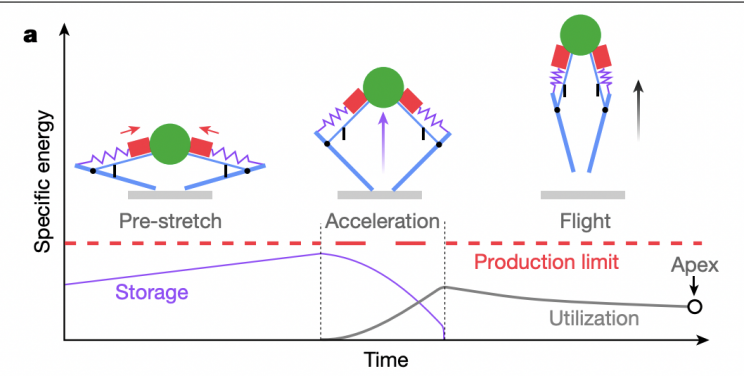
It was also found that a mix of rubber bands and carbon-fiber springs could store a huge amount of energy per mass.
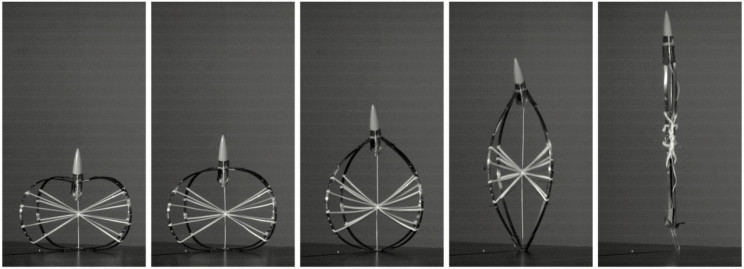
“This unexpectedly high ratio between spring and motor mass is a result of the relative energy limitations of these components: the energy density of the spring limits the robot’s jump height, whereas the work density of muscle limits the amount of energy that biological jumpers can store in their springs,” Bergbreiter explains.