In the field of sustainable construction, Sublime Cement emerges as a revolutionary contender, poised to disrupt traditional cement manufacturing processes.
Amidst various low-carbon and carbon-capturing concrete alternatives under development, Sublime Systems, a spinout from MIT, stands out. Its pioneering electrochemical approach to cement-making sets it apart, offering a “true zero carbon” solution that eliminates carbon emissions at critical stages of the production process.
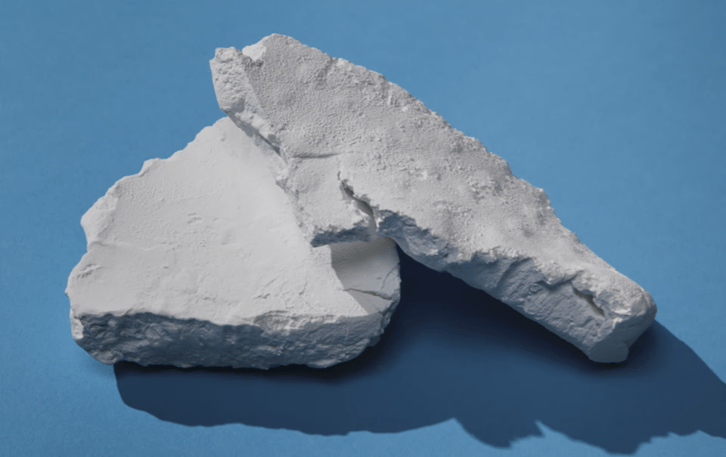
Traditional cement production involves heating limestone to about 1,400°C (2,552°F) using fossil fuels, a primary source of emissions. Yet, limestone contains approximately 50% carbon dioxide by weight, and the release of CO2 during heating is challenging to capture, as it mingles with flue gases.
Sublime’s groundbreaking approach centers on electrochemistry. Hydrogen and oxygen gases are generated through near-neutral pH water electrolysis, creating a pH gradient between electrodes. Calcium-bearing minerals react with the acid formed at the anode, producing dissolved calcium ions that migrate toward the cathode. Upon reaching a pH level of at least 12.5, these ions react with the base generated at the cathode, forming solid calcium hydroxide, also known as builder’s lime or slaked lime.
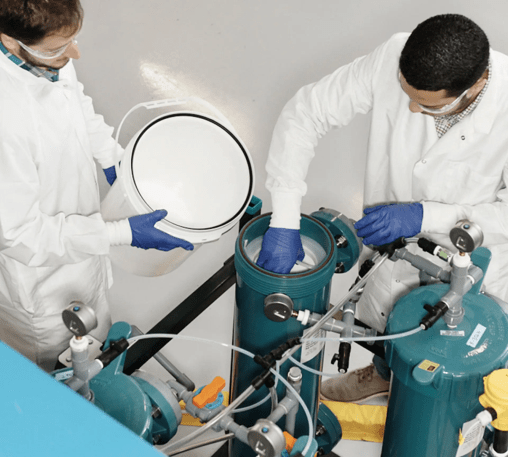
This calcium hydroxide serves as a direct replacement in traditional cement manufacturing processes. Sublime has refined this process for enhanced energy efficiency, eliminating hydrogen production, separating oxygen and CO2 gas streams, facilitating continuous lime extraction, and employing off-the-shelf electrolysis equipment.
The versatility of Sublime’s process allows for the utilization of various feedstocks. In cases where low-grade limestone is economically viable, it can be utilized. To achieve zero carbon cement, the process can extract pure calcium from impurities in materials like silica, magnesium, iron, or aluminum, refining them into higher-grade components. Crucially, this entire process occurs at room temperature, eliminating the need for combustion furnaces or electric heating.
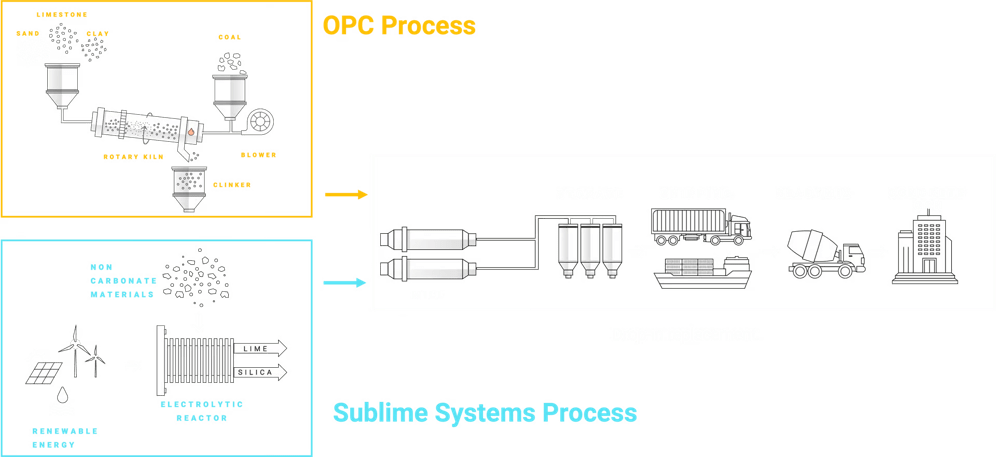
Sublime proudly touts its product as the “only fossil-fuel-free, scalable, drop-in replacement for traditional cement in concrete.” Notably, Sublime Cement has earned the ASTM C1157 designation, which sets industry performance standards based on parameters such as strength, durability, shrinkage, and more. This achievement enables Sublime Cement to comply with major American and international building codes.
Despite the immense potential of zero-carbon cement, a key challenge remains: cost competitiveness. Sublime aims to achieve cost parity with traditional Portland cement production within the next eight to ten years. In the short term, while its process may be somewhat costlier than traditional methods, it anticipates that the cost will still be lower than Portland cement plus carbon capture.
Sublime’s journey has evolved from a gram-scale research lab model at MIT to a facility capable of producing approximately 100 tons of cement annually. The next milestone is a demonstration plant, scheduled for commissioning by the end of 2025, with production commencing in 2026. Subsequently, plans include the establishment of a full-scale commercial cement manufacturing facility, producing around a million tons per year by 2027-28, ultimately aiming for global deployment in the 2030s.
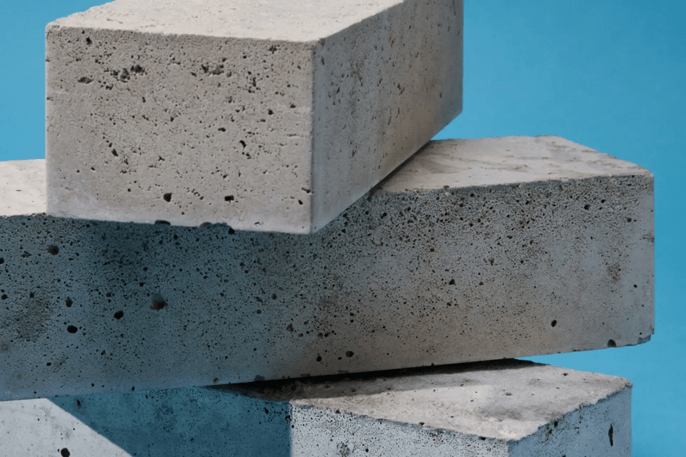
As the world grapples with the imperative of sustainable construction materials, Sublime Cement emerges as a beacon of innovation. Its true zero-carbon approach, scalable technology, and commitment to achieving cost competitiveness offer hope for a greener, more sustainable future in the construction industry. Collaborative efforts among stakeholders, including building owners, architects, engineers, and materials suppliers, will play a pivotal role in driving the adoption of low-carbon cement and addressing the urgent need for sustainability in construction.
Source: Sublime Systems