A new type of helmet is in the works. It uses sensors to determine when the shaking becomes too much for the human body to handle. When that happens, the helmet sounds an alert so the driver may remain out of danger.
Intended for use by drivers of rough-riding machines, the helmet is designed for the drivers of heavy-duty machines such as excavators and bulldozers. It was designed by a team at Germany’s Fraunhofer Institute for Structural Durability and System Reliability.
Installed with a flexible piezoelectric sensor, the helmet looks like a regular one but is nothing like it. The sensor is installed at the internal fastening strap and atop the wearer’s head.
The sensor works with the piezoelectric effect. It is made from an aluminum-coated polypropylene foam shaped like a thin foam. It works on a simple principle: when the vibrations or shakiness of the driver’s helmet increases, the film’s deformity rises, subsequently sending electrical signals through its receptors. The higher the voltage, the more significant the deformation.
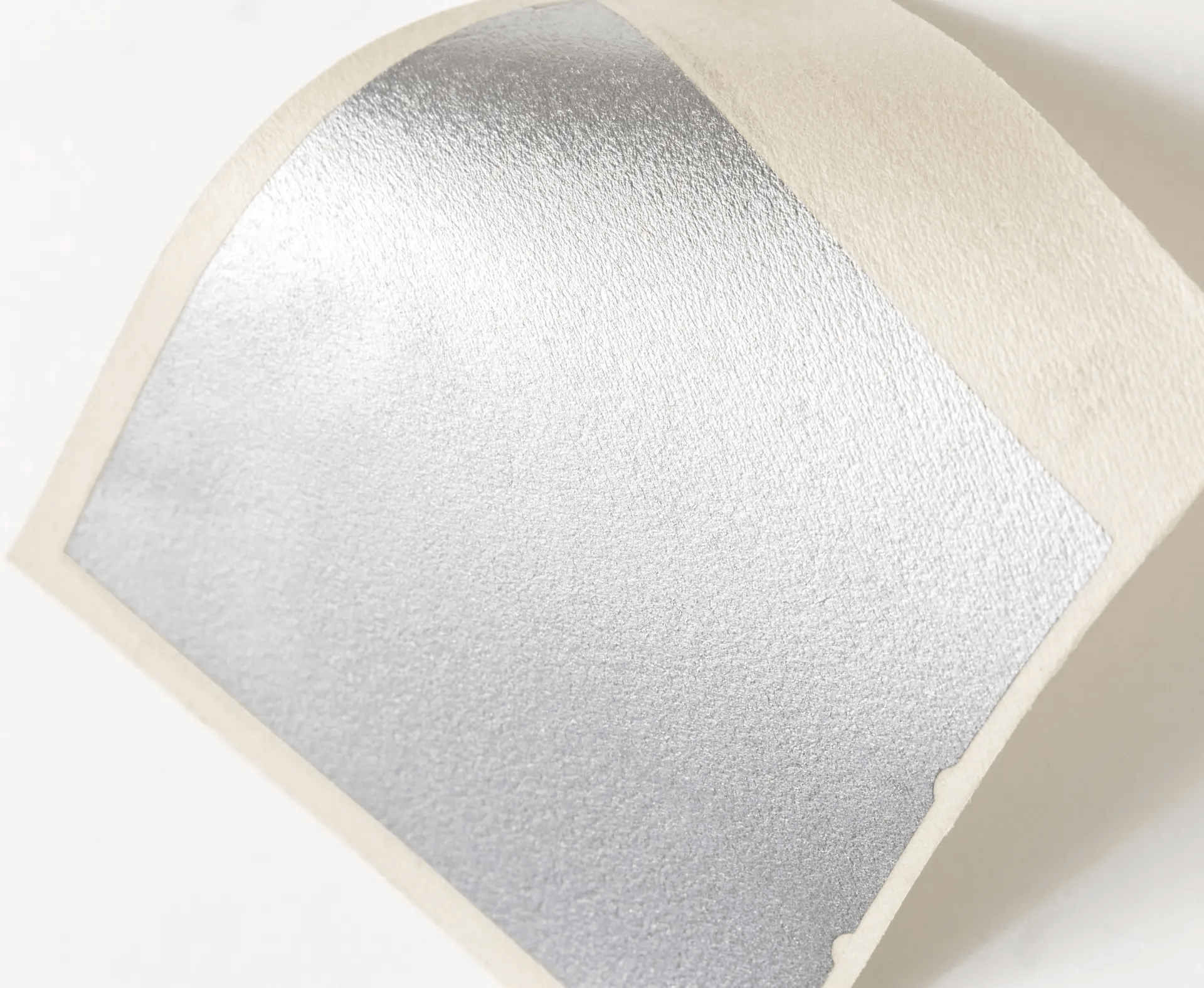
The software then analyses the data and alerts the driver if dangerous levels of shaking have been achieved. The driver can then take a break to stay out of harm’s way.
The sensor in the helmet is a massive step toward worker safety as it ensures that labor involved in these rigorous jobs remains out of danger. The same sensor can also be installed in vehicles with an alert system so that the car controls the shakiness offered by the terrain.
“The whole-body vibrations to which construction machine drivers are exposed reach acceleration values of 0.2 m/s² to 1.5 m/s² on average; peak values can be considerably higher,” says Fraunhofer electromechanics expert Björn Seipel. “Our helmet sensor makes measuring the vibration load in everyday operations easy. Health protection can be considerably improved on this basis.”