Engineers at Stanford University have come up with a promising new technique that makes 3D printing more efficient and viable than before. The technique is reportedly claimed to have been 5 to 10 times faster than the process used in the existing high-resolution printers currently available on the market. This is one of the ambitious and critical projects carried forward by the engineers at Stanford University that has the capability to make great strides in the field of additive manufacturing. This futuristic project deploys the use of different types of resins to amalgamate the formation of a single object. However, the findings of this research have been published in “Science Advances.”
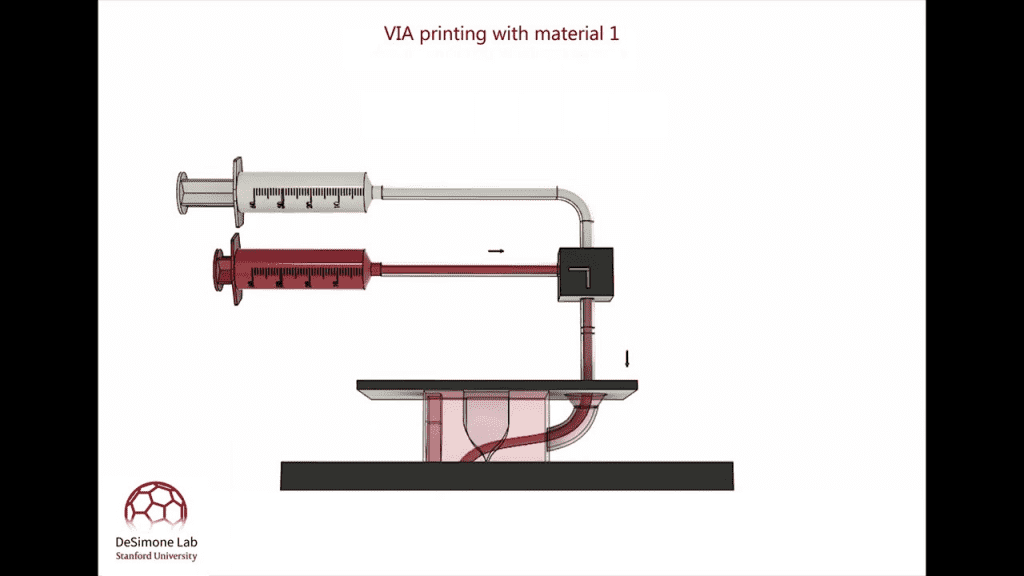
In this latest addition of 3D printing, researchers can now use thicker resins to produce different objects in order to enhance the electrical and mechanical characteristics of the resulting product. Also, the fast and efficient nature of this technique makes it stand out from all the existing technologies currently available. Joseph DeSimone, who is the Sanjiv Sam Gambhir Professor in Translational Medicine and professor of radiology and of chemical engineering at Stanford and author of the research paper, says, “This new technology will help to fully realize the potential of 3D printing. It will allow us to print much faster, helping to usher in a new era of digital manufacturing, as well as to enable the fabrication of complex, multi-material objects in a single step.”
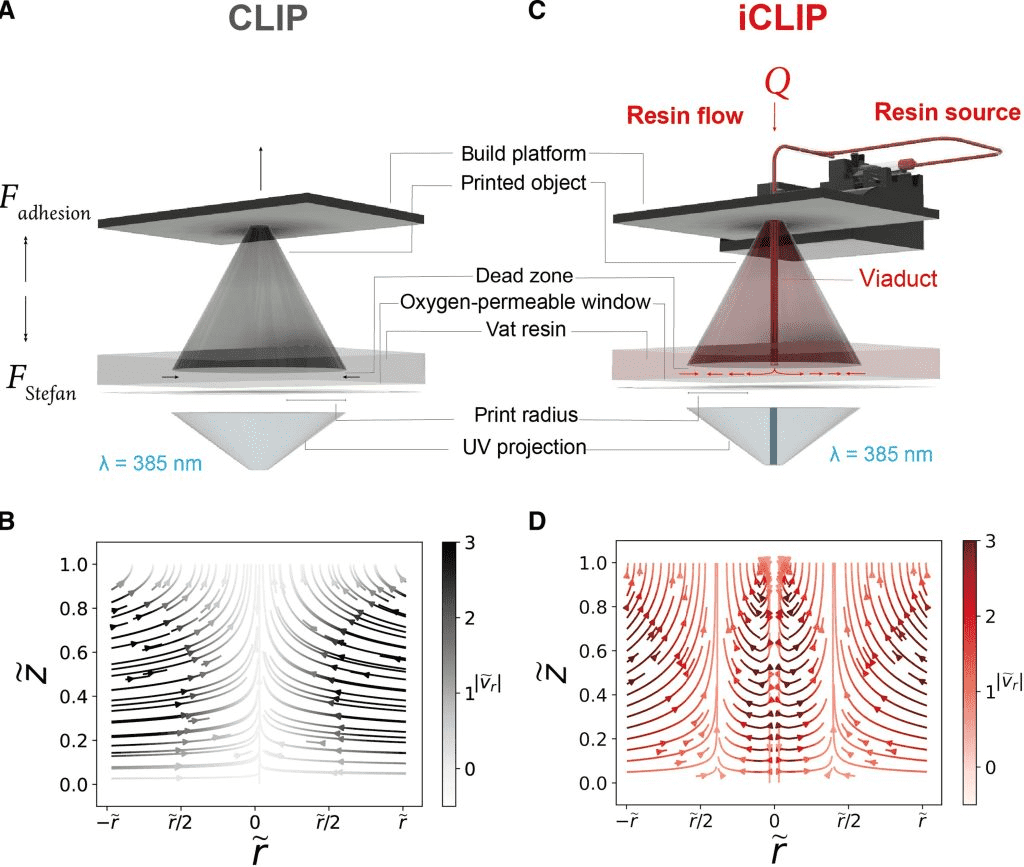
Coupled with this, it should be noted that DeSimone and his associates take off with developing this technique back in 2015 and they focused on improving the continuous liquid interface production or CLIP in it. The technique smoothly removes the completed object from a pool of thin resin material through CLIP. Here it has to take into consideration that a layer of oxygen leads to the development of a “dead zone” and due to this, the resin resists being converted into a solid form. In order to bridge this gap and transform it into the formed shape, engineers have transmitted some UV pictures through this pool, and in this way, the resin comes to its shape.
According to Gabriel Lipkowitz, who is a Ph.D. student in mechanical engineering at Stanford and the lead author of the paper, “The resin flow in CLIP is a very passive process – you’re just pulling the object up and hoping that suction can bring material to the area where it’s needed. With this new technology, we actively inject resin onto the areas of the printer where it’s needed.” He further stated, “The ability to make objects with variegated material or mechanical properties is a holy grail of 3D printing. The applications range from very efficient energy-absorbing structures to objects with different optical properties and advanced sensors.”
Also, researchers evaluated the performance characteristics of these resins having different colors by putting them into three different syringes. It is remarkable that the researchers achieved the milestone by printing samples of different historical monuments from their respective nations. Each monument was printed in the color of its national flag. “They have printed Independence Hall in the red, white, and blue of the United States and Saint Sophia Cathedral in the blue and yellow of Ukraine.” To that end, this 3D-printing technique has emerged and become a scientific mainstream.