Researchers have created a novel way to reduce the environmental impact of the steel sector while recycling the hazardous waste from the manufacture of aluminum. This creative method uses hydrogen to turn the dangerous red mud—a waste product from the production of aluminum—into green steel in just ten minutes.
An astounding 198 million tons of red mud, or bauxite waste, are produced by the aluminum industry each year. Red mud is infamous for having a high alkalinity level and a dangerous heavy metal load. The means of disposal, which are mostly large landfills, incur high processing expenses, which exacerbate environmental issues. Meanwhile, the steel sector, which contributes 8% of the world’s carbon dioxide emissions, is expected to see a 60% increase in demand by the year 2050.
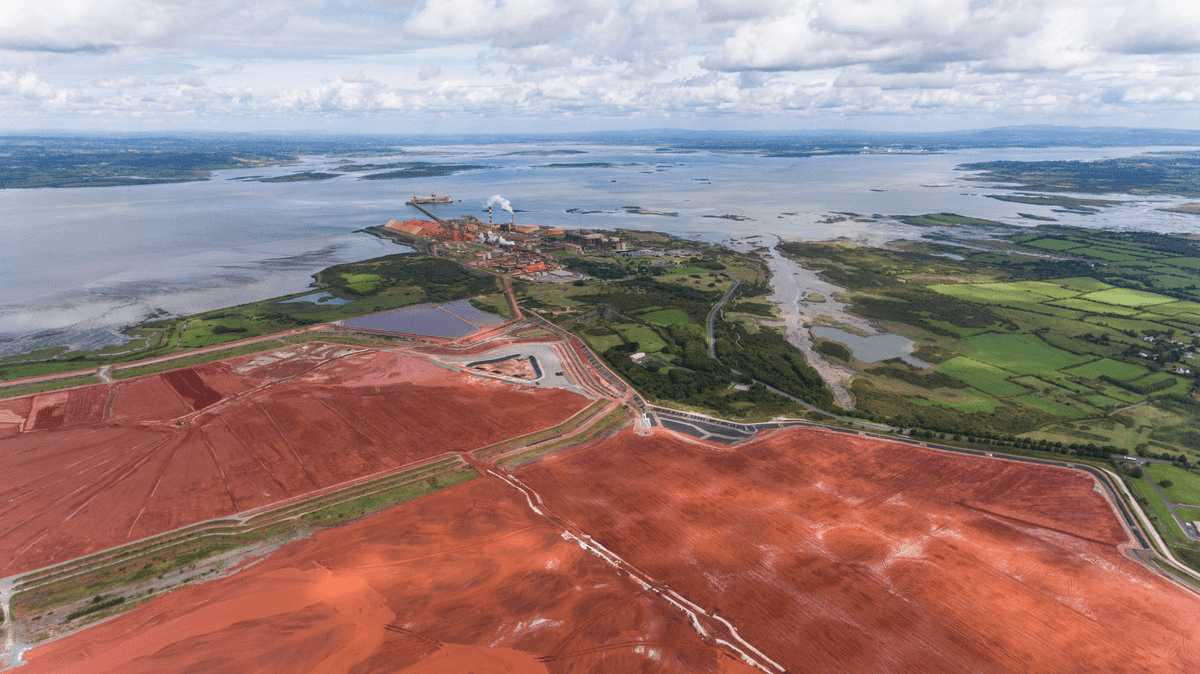
Scientists from the Max-Planck-Institut für Eisenforschung in Germany have pioneered a solution to this dual crisis. By leveraging red mud’s iron oxide composition, they’ve devised a process wherein plasma, infused with hydrogen, swiftly liquefies the mud in an electric arc furnace. This process yields exceptionally pure iron, directly applicable in steel production. Moreover, the residual metal oxides can be repurposed into glass-like materials for construction.
Prior attempts at red mud utilization involved coke, yielding contaminated iron and substantial carbon emissions. In contrast, the new approach employs green hydrogen as a reducing agent, mitigating greenhouse gas outputs. According to lead author Matic Jovi?evi?-Klug, this method could potentially save nearly 1.5 billion tons of CO2 emissions while neutralizing toxic heavy metals.
Further studies aim to explore the recovery and reuse of valuable metals embedded within the red mud. Economically, the process becomes viable if the mud contains a minimum of 35% iron oxide. Factoring in costs of green hydrogen, electricity, and landfilling, a competitive iron yield necessitates a 30-40% iron oxide concentration.
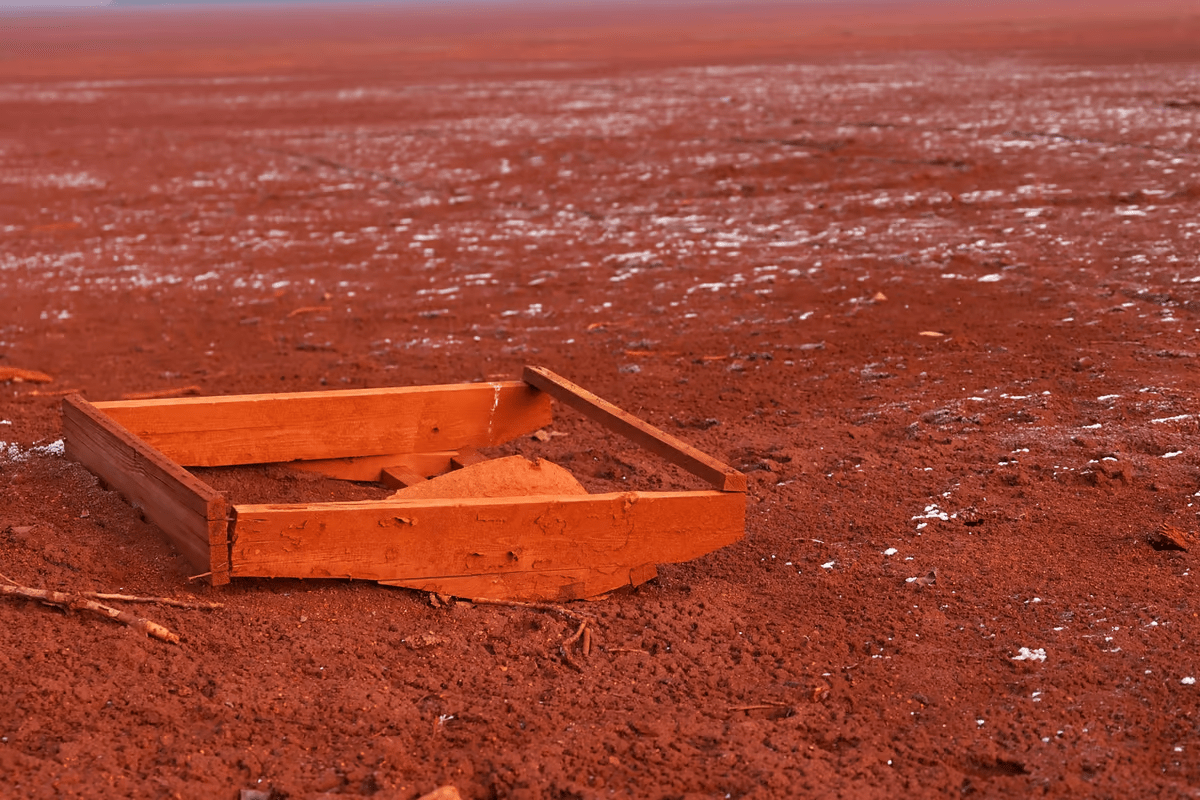
Importantly, this method aligns with existing infrastructure, requiring minimal industry adaptation. Co-author Dierk Raabe emphasizes the importance of economic viability, urging industry stakeholders to embrace this transformative technology.
The advent of green steel from red mud not only offers a sustainable solution to waste management but also holds the promise of reshaping the steel industry’s ecological footprint. As environmental imperatives drive industrial innovation, the adoption of such pioneering techniques stands as a beacon of progress towards a greener, more sustainable future.