Even though Lithium metal batteries with solid electrolytes are lightweight, inflammable, pack a lot of energy, and can be recharged very quickly, they have been slow to develop due to mysterious short-circuiting and failure. A team of members from Stanford University and SLAC National Accelerator Laboratory has come up with a new battery technology that solves this issue.
This issue of failing electrolytes is not new and many have been studying this for years. Some say the unintended flow of electrons is to blame, while others point to chemistry. Yet others theorize different forces are at play.
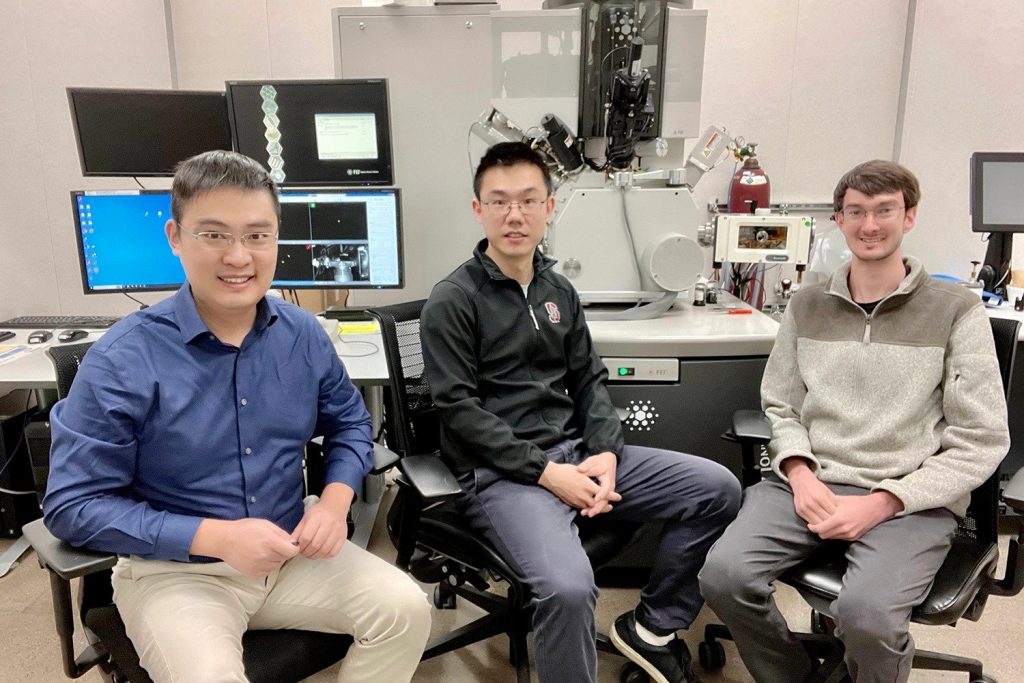
According to the team, the issue was down to mechanical stress, which was induced while recharging the batteries. “Just modest indentation, bending or twisting of the batteries can cause nanoscopic issues in the materials to open and lithium to intrude into the solid electrolyte causing it to short circuit,” explained William Chueh, senior study author and an associate professor at Stanford Doerr School of Sustainability.
“Even dust or other impurities introduced in manufacturing can generate enough stress to cause failure,” said Chueh.
The main issues that develop here are the tiny cracks that are prone to develop on the surface of ceramic materials. Throughout over 60 experiments, it was proved that ceramic material develops “nanoscopic cracks, dents, and fissures, many less than 20 nanometers wide”. According to the team, these inherent fractures open during fast charging, allowing lithium to intrude.
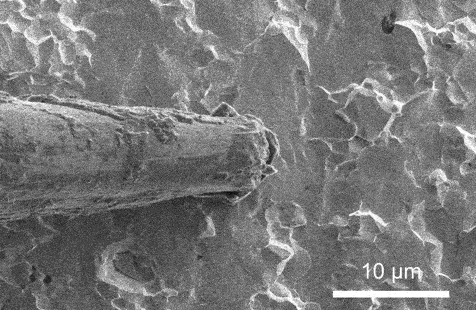
In short, it all comes down to mechanical stress, especially during recharging. Ceramic materials are excellent in transporting lithium ions and separating the two electrodes that store energy and most importantly, they are fireproof.
“It’s a little like the way a pothole appears in otherwise perfect pavement,” Xin Xu, one of the co-lead authors of the study explained. “Through rain and snow, car tires pound water into the tiny, pre-existing imperfections in the pavement producing ever-widening cracks that grow over time.”
With their new understanding in hand, Chueh’s team is looking at ways to use these very same mechanical forces intentionally to toughen the material during manufacturing, much like a blacksmith anneals a blade during production. They are also looking at ways to coat the electrolyte surface to prevent cracks or repair them if they emerge.