Amit Goyal, a distinguished professor in the US Department of Chemical and Biological Engineering at the University at Buffalo, is leading a research team that has created the highest-performing high-temperature superconducting (HTS) wire in the world. This accomplishment is ground-breaking. This wire functions at temperatures that are higher than the absolute zero temperatures needed by conventional superconducting materials, ranging from -451 to -321 degrees Fahrenheit (-268 to -196 degrees Celsius).
HTS wires are pivotal for future energy infrastructure due to their ability to transmit electricity with zero resistance. Beyond power transmission, they hold potential for doubling the output of offshore wind farms, constructing superconducting magnetic energy storage systems, and advancing nuclear fusion reactors, as well as next-generation imaging and spectroscopy techniques. However, the high cost of producing these wires has been a limiting factor.
In a significant advancement, researchers at the University at Buffalo combined two cutting-edge technologies—ion-beam assisted deposition (IBAD) and nanocolumnar defects—under Goyal’s leadership. This innovative approach allows insulating or superconducting materials to be incorporated into the wire, creating vortices that enable higher supercurrents to flow.
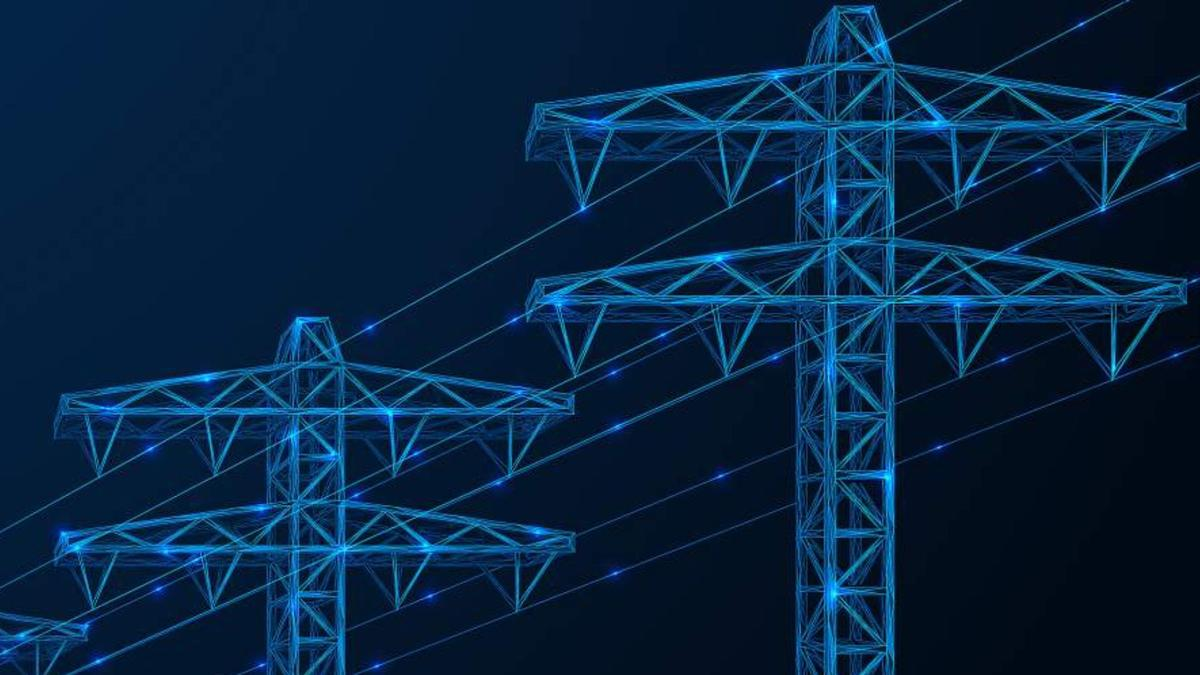
Using a pulsed laser deposition system, the team created an HTS film on a rare-earth barium copper oxide (REBCO) wire. Advanced microscopy at the Canadian Center for Electron Microscopy and superconducting property measurements at the Università di Salerno characterized the wire’s unique nanocolumnar and atomic-scale defects.
The result is a wire that demonstrates unprecedented performance, carrying 190 million amps per square centimeter at 4.2 kelvin without an external magnetic field. Even at 20 kelvin, the wires carried 150 million amps per square centimeter. The HTS film’s thickness was only 0.2 microns, yet it carried currents typically achieved by wires ten times thicker.
Goyal emphasized that this achievement could guide industry toward optimizing production processes, making HTS technology more cost-effective and unlocking its full potential for large-scale applications.