Researchers at the Department of Energy’s Oak Ridge National Laboratory have created one of the “toughest materials ever reported” in the form of a reusable adhesive. The adhesive was made from everyday household plastics.
According to ORNL scientists, the technology adapts to handle enormous loads, withstand tremendous stress and heat, and reversibly attach to various glass, aluminum, and steel surfaces.
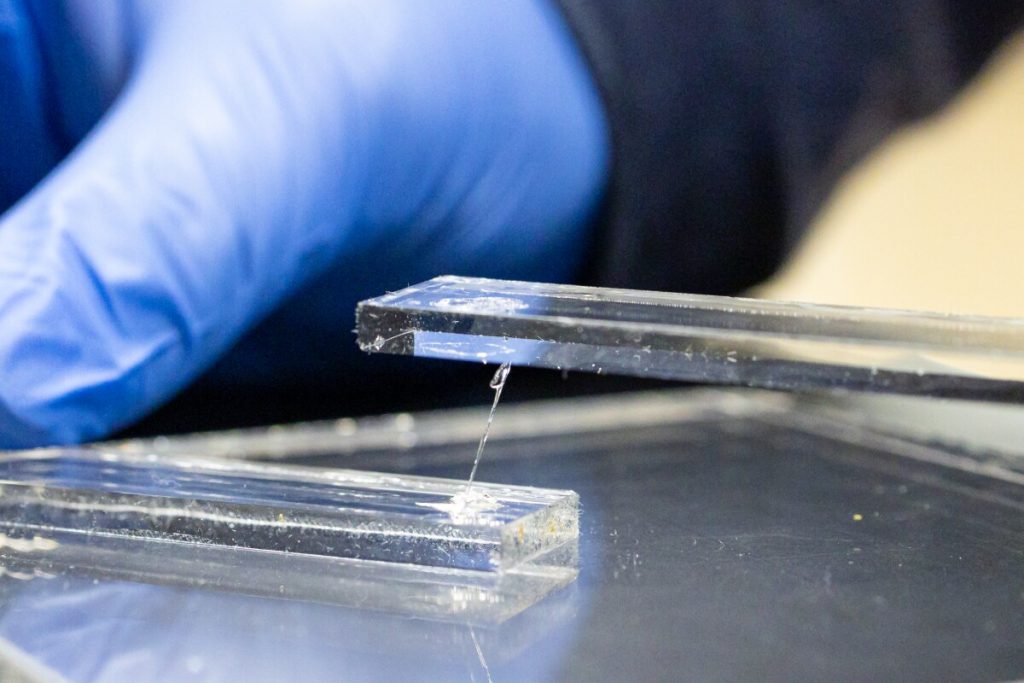
But how did they manage it? Researchers at ORNL intended to upcycle polystyrene-b-poly(ethylene-co-butylene)-b-polystyrene, or SEBS, a rubbery polymer material that is simple to make but not designed for solid stickiness. As a result, they repurposed it and functionalized it to make it more durable.
“The goal of upcycling is to add value to common plastics produced in high volume for general and often disposable applications, such as food containers, toys, and household items,” ORNL said.
The team altered the chemical structure of SEBS “with dynamic crosslinking to make it more robust, as well as to create reuse pathways for plastics, beyond traditional recycling, that enhance their performance for new and specialized applications.”
Crosslinking can be a strong bridge between structures that might otherwise be incompatible. In this study, boronic esters were employed to bind SEBS to silica nanoparticles, or SiNP, a filler material used to strengthen polymers. A new crosslinked boronic ester-SiNP composite material is the product.
Crosslinked bonds travel within the material to enable diverse capabilities, according to ORNL, and bind to surfaces so strongly that a little square centimeter may transport roughly 300 pounds.
The sturdiness of the technique was tested by attempting to remove materials forcefully, and the results were astounding, exceeding all commercial adhesives tested in the research.
“The material was so tough in adhering to glass, in fact, that glass fractured before the sample debonded,” ORNL stated.
“The approach also enhanced thermal stability to 400 degrees Fahrenheit, making the adhesive attractive for ambient and high-temperature applications.”
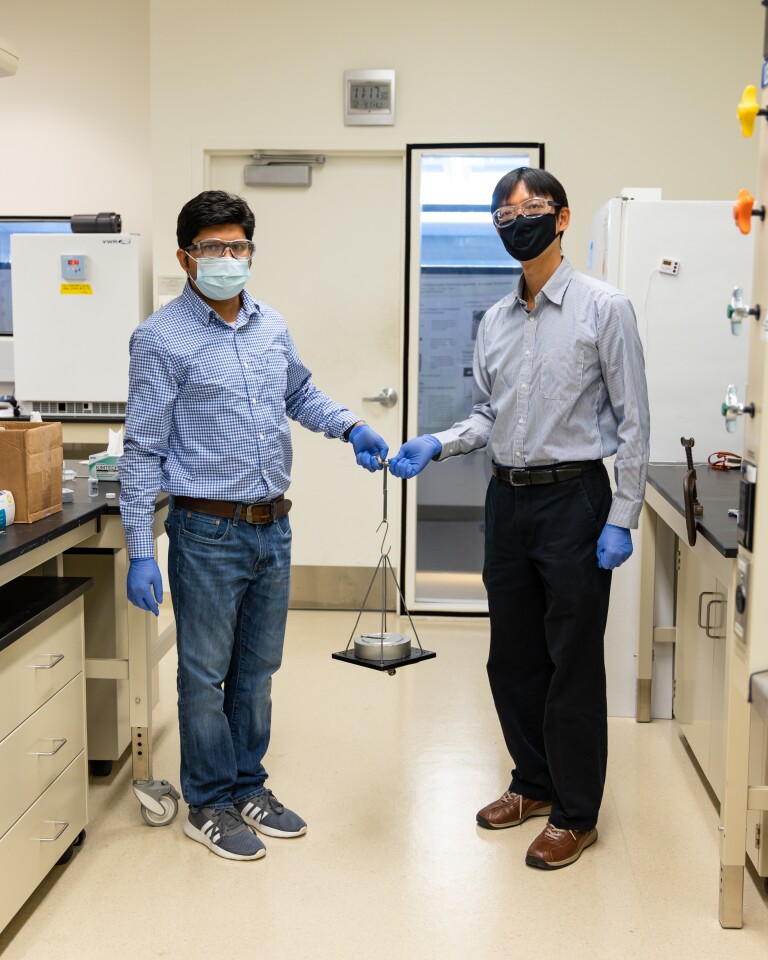
According to ORNL researchers, the technology expands the range of uses for aerospace, automotive, and construction adhesives.
“There are benefits to industry and the environment to save resources and reduce waste. By design, this adhesive allows you to make repairs or correct costly mistakes and can be reprocessed for new uses in very challenging applications,” lead author Md Anisur Rahman, who works within ORNL’s Chemical Sciences Division, said.
ORNL stated the team intends to commercialize the technique and is experimenting with dynamic crosslinking with different fillers to develop tough adhesives suited for only certain bonding surfaces and purposes.
The research was published in the journal Science Advances.
Source: Oak Ridge National Laboratory