ThinkOrbital, a United States company, has made history with the world’s primary independent in-orbit welding system. It was carried out in the orbit through a payload dispatched on May 6 aboard SpaceX Falcon 9. The mission’s electron beam welder samples have come back to Earth where NASA and the European Space Agency will take them apart — all in order to find out more information about what microgravity does to the welding process: about how it can affect this technique under weightlessness.
A major breakthrough indeed, as emphasized by the company’s announcement: “Our journey has been nothing short of extraordinary, from the groundbreaking first-ever autonomous in-space weld to the historic return of flown-in-space electron-beam welder samples.” The goal of ThinkOrbital is to revolutionize in-space construction and satellite servicing through an innovative toolkit. This toolkit consists of various tools such as a robotic arm with different interchangeable end effectors for autonomous welding— among other instruments, a suite includes those for cutting and additive manufacturing.
The system uses electron beam welding (EBW) technology in addition to having X-ray cameras. Because of its extreme precision, lack of filler material requirement, and vacuum operation, EBW is especially well-suited for space applications. The technology is perfect for the extreme conditions of space since it can tolerate strong vibrations, sudden temperature fluctuations, and weightlessness. The manufacturer claims that EBW has the largest heat-affected zone, the strongest weld, can weld 30 centimeters of steel in a single pass, and has an energy efficiency of over 90%.
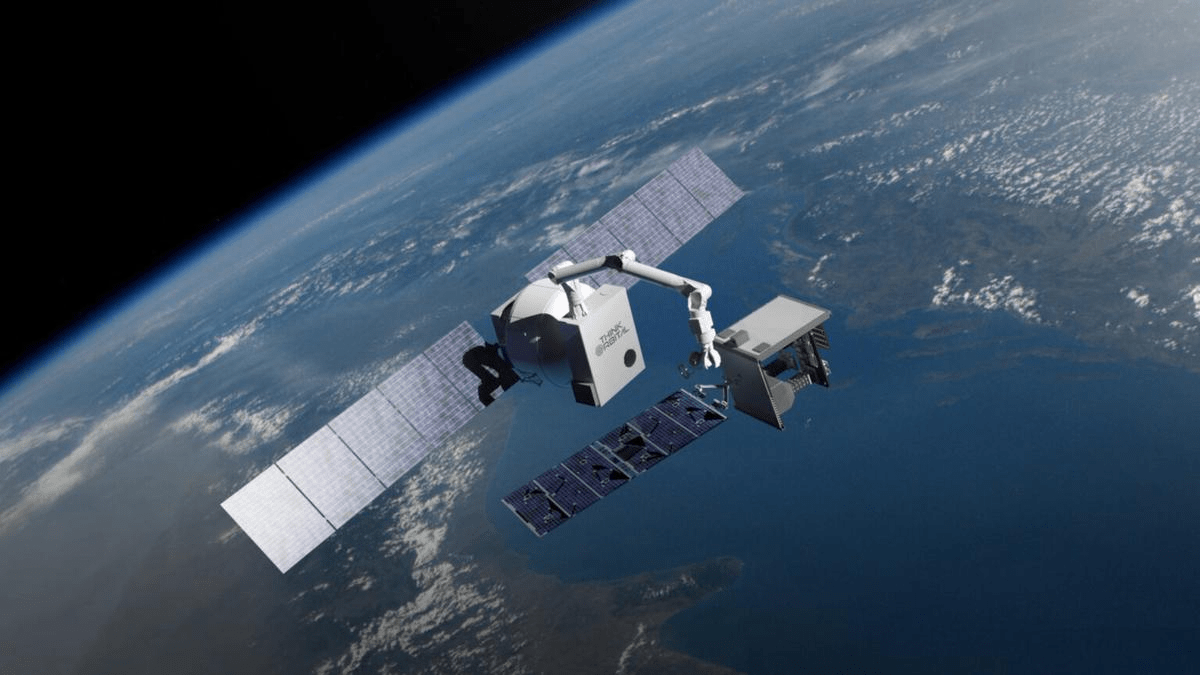
This innovative system holds the potential to enable the direct development of large space station modules, lunar habitat domes, and other structures. The orbital toolkit is still in development, aiming to pave the way for spacecraft repair and extend the lifespan of space assets, reducing the need for costly replacement missions.
In October, ThinkOrbital plans to test its high-tech robotic arm, equipped with an electron beam welder, in space. This welder gun can also generate X-rays to inspect objects in space, a capability that has caught the interest of the United States military for identifying orbital threats. ThinkOrbital has secured a U.S. Air Force Phase 1 Small Business Innovative Research contract to explore the feasibility of satellite-to-satellite X-ray inspection and plans to apply for Phase 2 funding.
Additionally, ThinkOrbital is developing the ThinkPlatform concept, a spherical structure that can be packaged flat and autonomously assembled in orbit using welding and additive manufacturing methods. This structure is expected to be four times larger than the International Space Station, marking a significant leap forward in space construction technology.
This innovative system holds the potential to enable the direct development of large space station modules, lunar habitat domes, and other structures. The orbital toolkit is still in development, aiming to pave the way for spacecraft repair and extend the lifespan of space assets, reducing the need for costly replacement missions.
In October, ThinkOrbital plans to test its high-tech robotic arm, equipped with an electron beam welder, in space. This welder gun can also generate X-rays to inspect objects in space, a capability that has caught the interest of the United States military for identifying orbital threats. ThinkOrbital has secured a U.S. Air Force Phase 1 Small Business Innovative Research contract to explore the feasibility of satellite-to-satellite X-ray inspection and plans to apply for Phase 2 funding.
Additionally, ThinkOrbital is developing the ThinkPlatform concept, a spherical structure that can be packaged flat and autonomously assembled in orbit using welding and additive manufacturing methods. This structure is expected to be four times larger than the International Space Station, marking a significant leap forward in space construction technology.