A team of EPFL engineers has come up with a 3D-printing method that uses light to make objects out of opaque resin in just seconds. This can have revolutionary applications in the biomedical industry, such as to make artificial arteries.
EPFL’s 3D printer is one of the fastest in the world. Whereas most 3D printers work by depositing a material layer by layer in a process known as additive manufacturing, the EPFL one uses a volumetric method. “We pour the resin into a container and spin it,” says Christophe Moser, a professor at LAPD.
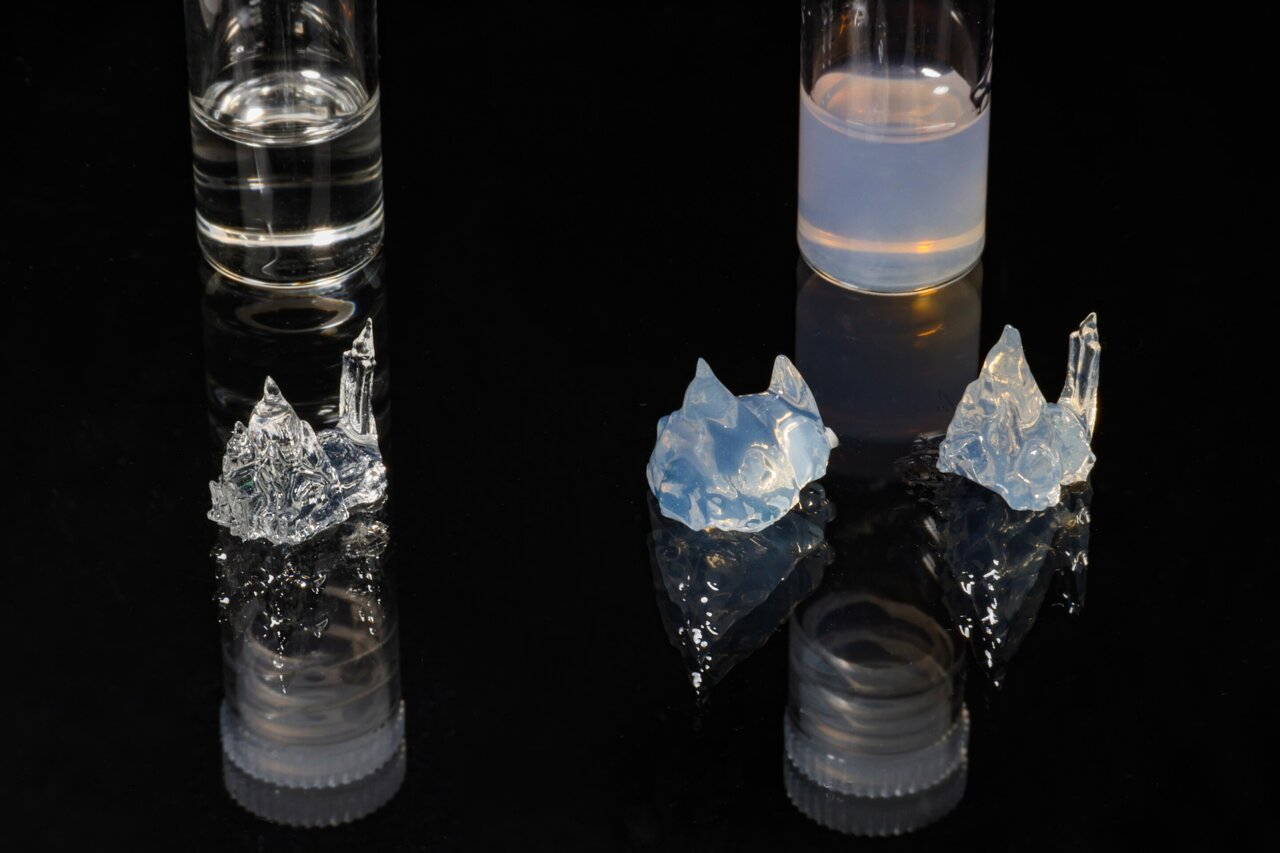
“Then we shine light on the container at different angles, causing the resin to solidify wherever the accumulated energy in the resin exceeds a given level. It’s a very precise method and can produce objects at the same resolution as existing 3D-printing techniques.” They tested this method by creating a tiny Yoda. It took just 20 seconds for them to make the figurine, versus around ten minutes for a traditional additive-manufacturing process.
The light rays are able to solidify the resin by interacting with a photosensitive compound contained in the plastic. “Our method works only if the light passes through the resin in a straight line without being deviated,” says Antoine Boniface, a postdoc at LAPD. “Until now we’ve always used transparent resin, but we wanted to see if we could print objects in the kind of opaque resin that’s used in the biomedical industry.”
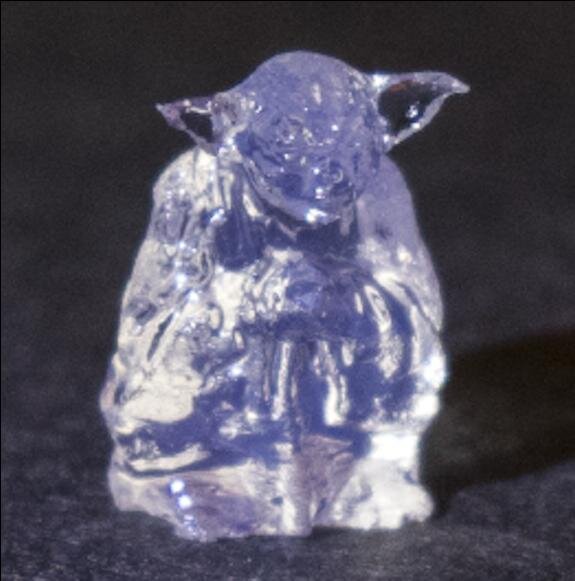
However, the limitation of this method is that the light doesn’t propagate smoothly, making it hard to accumulate the amount of energy needed for the resin to solidify. “With opaque resin, we lost a lot of resolution in the printed object,” says Jorge Madrid-Wolff, a Ph.D. student at LAPD. “So we tried to come up with a solution that would let us fabricate objects in this resin but without losing the advantages of our 3D printer.”
The solution they found was simple. First, they used a video camera to observe the light’s trajectory through the resin and then designed computer calculations to compensate for the light-ray distortion. They programmed their printer to run these calculations and correct the light rays as the printer operates. This allowed the engineers to print objects in opaque resin with almost the same precision as for transparent resin.
As a next step, the engineers hope to be able to print several materials at once and increase their printer‘s resolution from one-tenth of a millimetre to a micrometre. The engineers’ research has been published in Advanced Science.