In a forward-thinking proposal, Swiss researchers are advocating for the use of autonomous robotic hydraulic excavators to build dry stone walls on the Moon.
This innovative approach aims to protect lunar bases from the intense rocket exhaust and dust clouds that accompany spacecraft launches. The proposed stone walls, made from lunar materials, offer a cost-effective alternative to transporting building materials from Earth.
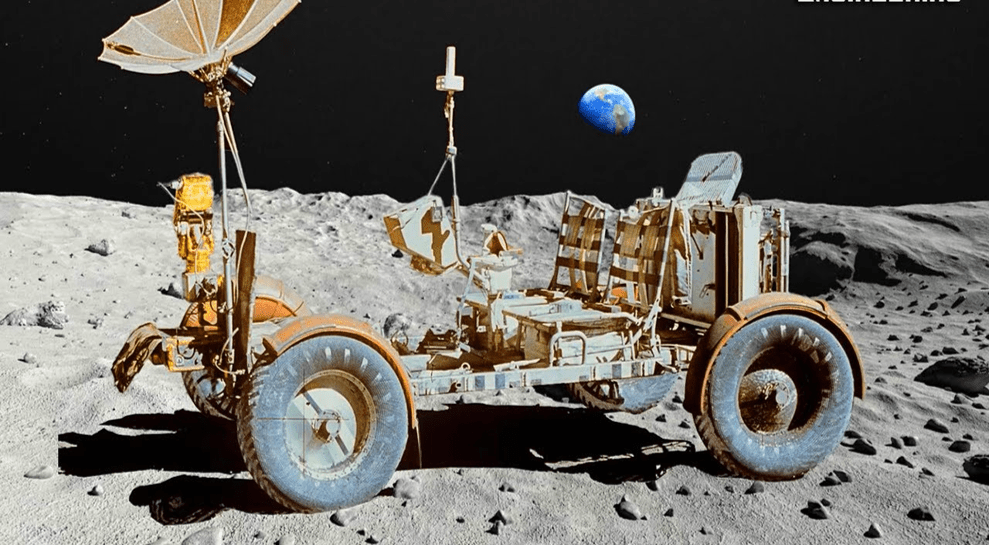
The envisioned walls would form a protective ring with a radius ranging from 164 to 328 feet (50 to 100 meters), addressing the issues encountered during past missions. For example, the Apollo 12 mission revealed damage to lunar equipment from rocket exhaust and dust when it returned parts of the Surveyor III lander, which had been on the Moon since 1967.
As NASA’s Artemis mission aims to establish a permanent lunar colony, and SpaceX’s Starship Human Landing System facilitates transport between the Moon and orbit, the problem of lunar dust becomes increasingly critical. Studies show that this dust can affect areas well beyond launch sites, making the construction of a protective blast shield essential.
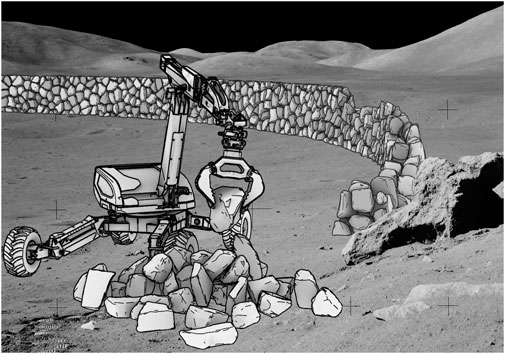
The researchers propose constructing these walls using boulders found on the Moon, leveraging existing resources to avoid the high costs of importing materials. They suggest a quarter-ring structure to offer targeted protection where it’s most needed. To determine the feasibility, they analyzed images from the Lunar Reconnaissance Orbiter (LRO) to identify suitable boulders and estimate the amount needed—approximately 250 cubic meters for a quarter-ring segment.
Several challenges must be addressed to make this lunar construction method viable. One concern is whether the gaps in a dry stone wall, due to the irregularity of unprocessed boulders, will affect its performance as a blast shield. Simulations and experiments under lunar conditions are needed to assess this.
Additional challenges include the logistics of material collection, construction time, and the energy requirements for recharging the robotic excavators. Possible solutions include autonomous energy harvesting, centralized recharging stations, or using radioisotope thermoelectric generators (RTGs).
The study is published in Frontiers in Space Technologies.