NASA has been making all the headlines as it recently tested its new jet engine technology which has enhanced its rocket’s fuel efficiency manifolds.
To understand how NASA achieved this feat, you first have to know some basics of fluid mechanics. Jet engines are typically placed away from the aircraft’s body to avoid the boundary layer build up around the wings. The boundary layer is a thin layer of air which moves over the surface of an aircraft wing or airfoil. This layer has a significant contribution to fluid dynamics of the aircraft.
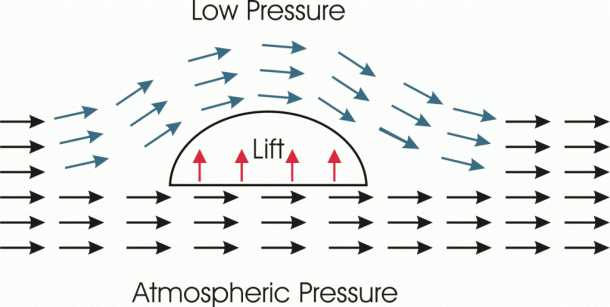
The results have been nothing short of astonishing, with the fuel efficiency increasing by four to eight percent, more than any other advanced engine designs.
Of course, the change in the position of the engine has its challenges. Placing the engine intake inside the boundary layer makes the incoming air turbulent, leading to a lot of distortion. The turbulent air affects the operational efficiency of the fan as it puts high amounts of stress on it. To cater for this, NASA engineers have also designed a much stronger fan that can withstand the distortion without compromising the efficiency.
Currently, the propulsion engine is being tested in a 2.5-meter by a 2-meter wind tunnel, under United Technologies Research Center and Virginia Polytechnic and State University.
“Studies backed by more detailed analyses have shown that boundary layer ingesting propulsors have the potential to significantly improve aircraft fuel efficiency,” says David Arend, a BLI propulsion expert at NASA Glenn.“If this new design and its enabling technologies can be made to work, the BLI propulsor will produce the required thrust with less propulsive power input. Additional aircraft drag and weight reduction benefits have also been identified.”
The world now holds its breath to see if NASA can overcome the problems with the BLI and materialize this high-efficiency engine to usher a new era in space exploration.
We would appreciate your feedback in the comments’ section below!