In 2013, Elon Musk unveiled the Hyperloop concept—a revolutionary transportation system utilizing near-vacuum tubes to propel passengers between cities at speeds reaching 1,000 km/h (621 mph). Despite Musk’s success with electric vehicles and reusable rockets, Hyperloop struggled against daunting technical and financial barriers, including airtight sealing challenges, temperature fluctuations, and the integration of high-speed maglev technology into existing infrastructure. However, a recent breakthrough in China suggests that the dream of near-supersonic ground travel may still have a future.
In 2024, Chinese engineers constructed a 2 km (1.2-mile) test track in Yanggao County, Shanxi province, to advance near-vacuum maglev transportation. A team led by master engineer Xu Shengqiao at the China Railway Engineering Consulting Group (CREC) pioneered a hybrid steel-concrete tube design, reinforced with epoxy-coated rebar and corrugated steel expansion joints. This innovative construction method combines the tensile strength of steel with the compressive durability of concrete, ensuring airtight stability under extreme temperatures ranging from sub-zero conditions to 45°C (113°F) summers.
Musk’s original Hyperloop plan relied on large steel tubes, which suffered from structural vulnerabilities such as leaks and excessive drag at higher speeds. In contrast, the Chinese team developed techniques to reduce energy loss by over 30%. A key improvement involved incorporating low-carbon steel grids, which mitigate the eddy currents that typically hinder maglev systems when operating above 1,000 km/h. The result: a vacuum-sealed corridor robust enough to support near-supersonic speeds while sidestepping the heat and pressure issues that plagued previous Hyperloop designs.
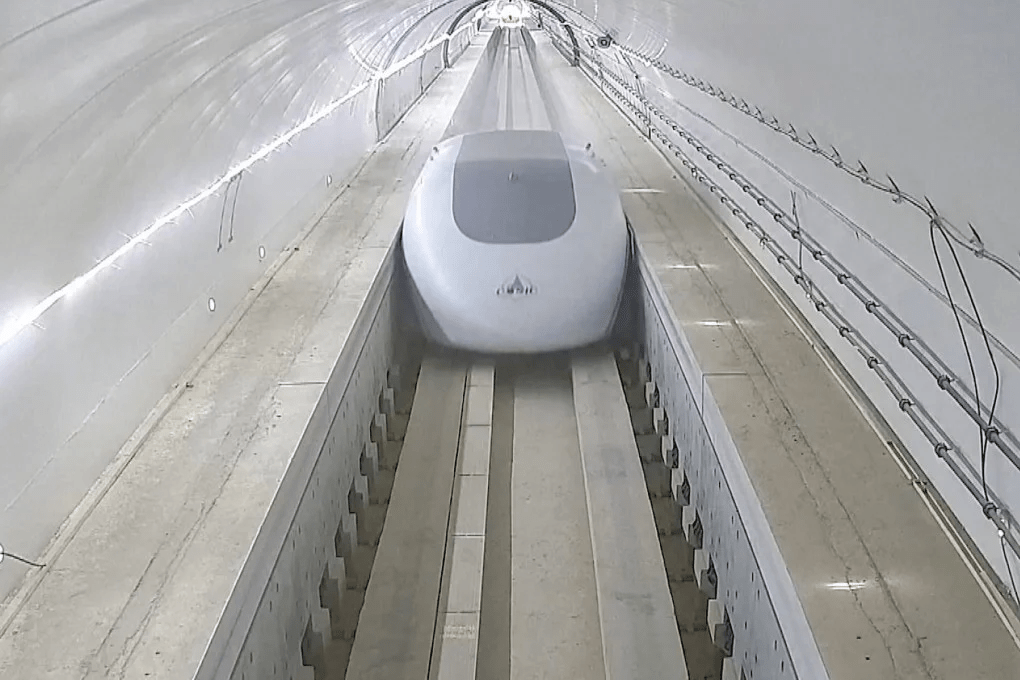
Developing a functional near-vacuum transportation system required rethinking conventional materials. Standard steel reinforcements in concrete are prone to warping or cracking in low-pressure conditions, while traditional concrete can deteriorate as internal air pressure nears zero. To counteract these risks, the Chinese research team incorporated basalt-fiber concrete, glass-fiber reinforcements, and pre-vacuum curing techniques.
On July 22, 2024, Xu’s team successfully tested a levitating vehicle on the maglev track within a partial vacuum. The test featured laser-guided sensors and AI-driven magnetic dampers to ensure stability, while a network of distributed vacuum pumps regulated pressure levels. Additionally, critical safety mechanisms—including emergency airlocks and reinforced passenger cabins—were implemented to address the same concerns that previously hindered Musk’s Hyperloop trials.
The CREC team now has a functioning 2 km test track and a scalable blueprint for expansion. Prefabricated tube segments, which reduce costs by up to 60% compared to traditional steel pipeline construction, make large-scale development more feasible. However, commercial deployment would require significant investment—potentially hundreds of billions of yuan. Engineers are still tackling key challenges, such as thermal expansion over long distances and the design of rapid emergency response systems.
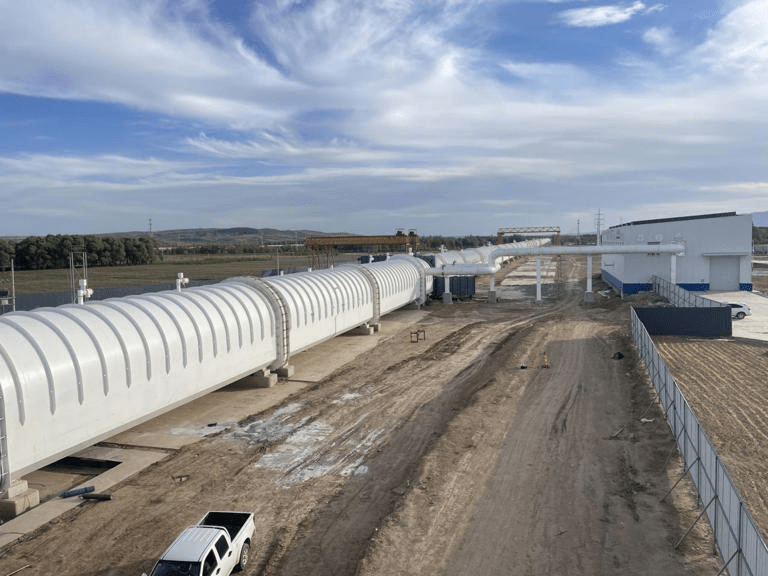
China’s experience in high-speed rail development may provide an advantage in bringing Hyperloop-like technology to life. Advanced welding automation, laser-guided surveying, and extreme precision in infrastructure engineering have already placed China at the forefront of rail transportation. Combined with cutting-edge superconducting materials and vacuum technology, these factors could position China as the leader in near-vacuum maglev travel.
While it remains uncertain whether the test line will evolve into a large-scale commercial project, one thing is evident: China has reignited the pursuit of near-supersonic land travel, demonstrating the determination and engineering prowess necessary to turn science fiction into reality.