3D printing revolutionized manufacturing after its development. However, it was not able to properly infiltrate the commercial applications market. The reason being that most printers take more than an hour to manufacture a small object. A new design from MIT engineers can very well change that as 3D printing gets a speed boost and now they can perform ten times faster than they did before.
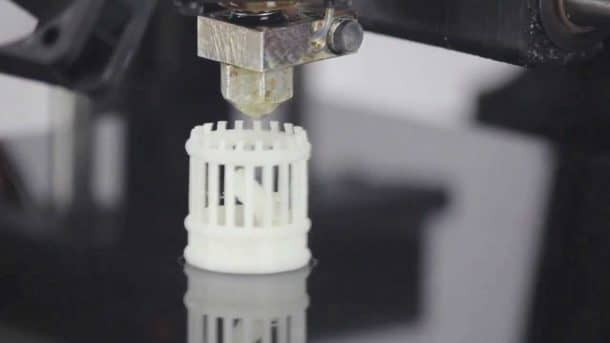
Associate professor of mechanical engineering at MIT, Anastasios John Hart, and former graduate researcher Jamison Go are behind this discovery. They focused on the three fundamental factors that were limiting the speed of an extrusion 3D printer. These factors are the speed of the moving printhead, the force with which the printing material is being pushed through the nozzle, and the rate the material can be melted to make it flow.
“Given our understanding of what limits those three variables, we asked how do we design a new printer ourselves that can improve all three in one system,” says Hart. “And now we’ve built it, and it works quite well.” What they did was redesign several mechanisms in the printhead as well as around it. They also added a laser to melt the plastic filament more rapidly.
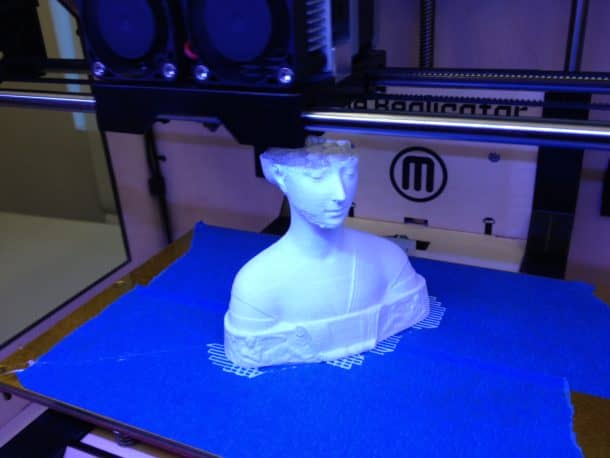
They called the modified system “FastFFF’ (fast fused filament fabrication), and this was up to ten times faster than the conventional printers. It only took minutes to print an object that took an hour before. The researchers claimed that this prototype system had a volumetric build rate of 127 cm3/hr, which is 7 times greater than the commercial 3D printers. They also said that this is not the full potential and at maximum extrusion rate, the volumetric build rate would be 282 cm3/hr, which is 14 times greater than we are used to.
Before they can celebrate their victory, they still have to fix one problem. Increasing the speed of the printing process meant that the layers were not being given enough time to cool before the next layer was printed on top of it. “We found that when you finish one layer and go back to begin the next layer, the previous layer is still a little too hot,” says Hart. “So we have to cool the part actively as it prints, to retain the shape of the part so it doesn’t get distorted or soften.”
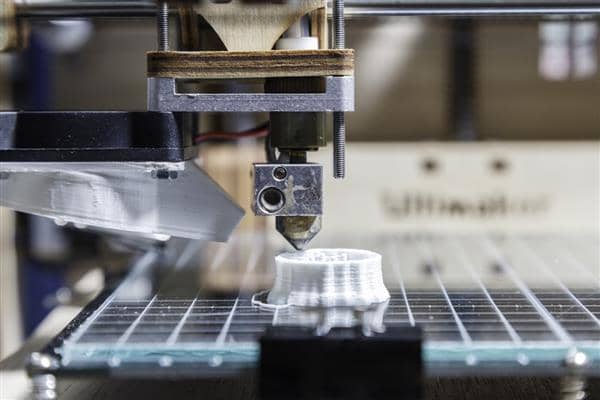
They are confident that this problem can be solved and once done, it will revolutionize the 3D printing industry and we will see a lot of commercials as well as industrial businesses switching to 3D printing.
“If I can get a prototype part, maybe a bracket or a gear, in 5 to 10 minutes rather than an hour, or a bigger part over my lunch break rather than the next day, I can engineer, build, and test faster,” adds Hart. “If I’m a repair technician and I could have a fast 3-D printer in my vehicle, I could 3-D-print a repair part on-demand after I figure out what’s broken. I don’t have to go to a warehouse and take it out of inventory.”
You can watch the printer in action here: